TITAN-PRODUKTION
- Allgemeine Informationen
- Vakuum-Lichtbogen-Umschmelzen von Titan
- Vakuum-Lichtbogen-Skull-Schmelzanlage
- Automatische Elektrodenzusammenbaustation (EAS)
- Digitalisierung
Titan wird seit den 1950er Jahren wegen seiner außergewöhnlichen Eigenschaften vor allem in der Luft- und Raumfahrtindustrie eingesetzt. Heutzutage kommen ca. 80% des produzierten Titans in der Luft- und Raumfahrtindustrie und 20% in anderen Sparten wie der Metalloberflächenbehandlung, der chemischen Verarbeitung, der Konsumgüterherstellung und in medizinischen Implantaten zum Einsatz. Um reines Titan oder reine Titanlegierungen aus einem Titanschwamm herzustellen, sind mehrere Verarbeitungsschritte notwendig, welche heutzutage über zwei unabhängige Produktionsrouten realisiert werden.
Bei der Titanschwamm-VAR-Produktionslinie muss der Titanschwamm mit verschiedenen Legierungszusätzen gemischt und verpresst werden. Die daraus resultierenden Presslinge werden dann mittels Plasma oder Elektronenstrahl-Schweißverfahren zu einer Schwammelektrode weiterverarbeitet, welche dann in einem Vakuum-Lichtbogen-Umschmelzprozess je nach Anforderung bis zu dreimal umgeschmolzen wird. Der fertige, solide Titanblock muss dann für die nachfolgende Weiterverarbeitung mittels Schmiede- und Walzverfahren zu Walzprodukten wie Stangen, Knüppel, Drähte, Rohre, Platten und Bleche geeignet sein.
Neben der klassischen Titanschwamm-VAR-Produktionslinie wird ebenfalls die Kaltherd-Umschmelzroute zum direkten Schmelzen, Veredeln und Gießen von Rohmaterialien wie Schrott, Schwamm und Legierungselementen zu Titanblöcken und -brammen eingesetzt. Bei diesem Verfahren werden die einzelnen Rohstoffe kontinuierlich oder chargenweisen in einen Kaltherd-Umschmelzofen eingebracht, wo sie durch eine hochenergetische Quelle (Elektronenstrahl oder Lichtbogen) geschmolzen werden. Nachdem die erzeugten Blöcke gegossen und erstarrt sind, können diese, je nach Anforderung, entweder im Vakuum-Lichtbogen-Umschmelzprozess nochmals umgeschmolzen oder konventionell durch Schmieden oder Walzen weiterverarbeitet werden.
Als Premiumlieferant für die Titan-Industrie mit mehr als 15 Jahren Erfahrung bieten wir unseren Kunden ein breites Portfolio an verschiedenen Technologien und Anlagen für deren individuelle Anforderungen. Das Ganze wird durch die Bereitstellung des kompletten Know-hows für die unterschiedlichen Routen der Titanproduktion abgerundet. INTECOs Experten unterstützen die Kunden, angefangen von der Durchführung einer Machbarkeits- und Vorinvestitionsstudie über das Engineering und die Evaluierung allgemeiner Anforderungen bis hin zur Inbetriebnahme der Anlagen. Darüber hinaus leisten INTECOs Experten Unterstützung bei der Produktzertifizierung, wie sie etwa für die Luft- und Raumfahrtindustrie benötigt wird. Das von INTECO entwickelte Prozess- und Produktionsmanagementsystem (IMAS) umschließt die gesamte Prozessroute und ermöglicht die Ausführung und Standardisierung von vordefinierten Abläufen sowie einen bedienerunabhängigen Prozess, welcher der Qualitätssicherung und auch den Anforderungen von Industrie 4.0 entspricht.
Durch das Vakuum-Lichtbogen-Umschmelz-Verfahren von Titan gewinnt man reines oder legiertes Titan mit hohem Reinheitsgehalt und von hoher Qualität. Dieses Umschmelzverfahren ist im Prinzip dem VAR-Umschmelzen von Stahl und Superlegierungen sehr ähnlich, jedoch gibt es bedeutende Unterschiede in Hinsicht auf die Prozesssteuerung und das Anlagendesign.
Basierend auf langjähriger Erfahrung mit der Vakuum-Lichtbogen-Technologie hat INTECO daher ein innovatives Ofenkonzept auf Stand der neuesten Technik für das Umschmelzen von Titan entwickelt. Darüber hinaus wurde in Zusammenarbeit mit der Montanuniversität Leoben ein umfassendes Simulationsmodel entwickelt. Dieses Simulationsmodell ermöglicht es, tiefere Einblicke in den komplexen Umschmelzprozess zu gewinnen und gibt unseren Kunden die Möglichkeit, ihr Prozess Know-how zu erweitern und die gesamte Produktion zu optimieren.
Unsere Technologie – Ihr Vorteil:
- Lichtbogen-Zentralisierungssystem auf neuestem Stand der Technik für eine homogene Verteilung des Magnetfeldes von Tiegelunter-bis Oberkante für höchste Sicherheit und verbesserte Metallurgie
- Hohe Produktivität durch vakuumdichte Absperrventile oberhalb der Schmelzstation
- Umfangreiches Prozess-Simulationsmodell, entwickelt in Kooperation mit der Montanuniversität Leoben
- Ganzheitliches INTECO Prozess- und Produktionsmanagementsystem (IMAS) für das gesamte Datenmanagement, die Datenspeicherung und die Definition der wichtigsten Prozessparameter
Im Hinblick der aktuellen Herausforderungen auf dem Titan- und Rohstoffmarkt und dem globalen Ziel, die CO2-Emissionen zu reduzieren, steigt auch bei Titanproduzenten weltweit der Trend, die Recyclingraten und Flexibilität in ihren Produktionsprozessen zu erhöhen. Um diesen Anforderungen gerecht zu werden hat INTECO das bereits bewährte Vakuum-Lichtbogen-Skull-Schmelz-Verfahren neu durchdacht und revolutioniert.
Neben dem klassischen Verfahren, in welchem eine Elektrode in einem wassergekühlten Kupfertiegel abgeschmolzen wird und die Schmelze danach in eine Gusskokille abgegossen wird, ist es in dieser neuartigen Anlage auch möglich, größere Mengen an Schrott zwischen den Abguss Zyklen in den Kupfertiegel zu chargieren. Mit dieser Technologie ist man somit in der Lage, bis zu 100% des eingesetzten Titanschrotts zu recyclen.
Eine Homogenisierung und Reinigung der Schmelze von nichtmetallischen Einschlüssen wird durch die große Menge flüssigen Materials sowie durch die lange Verweildauer in der Flüssigphase erreicht. Schwere Partikel sinken ab und verbleiben im erstarrten Rest, welcher nach dem Abgießen im Kupfertiegel verbleibt (dem sogenannten „Skull“).
Um größtmögliche Flexibilität zu gewährleisten, wurden bei dem neuartigen Anlagendesign zwei unterschiedliche Gießtechniken in einer Anlage kombiniert: Formgießen für Barren und Brammen und dynamisches Gießen (Schleudergussverfahren) von Feingussteilen.
Unsere Technologie – Ihr Vorteil:
- Option auf Verwendung eines doppelrunden Kaltwandtiegels (ovale Form) für erhöhte metallurgische Effizienz und Flexibilität hinsichtlich des Abguss Gewichts (> 1000kg)
- Fördersystem, um während des Prozesses chargenweise Rohmaterial oder verschiedene Legierungsmaterialien in den Kupfertiegel zu fördern, für eine bis zu 100%ige Recyclingrate von Titanschrott
- Kombination zweier Gießtechniken in einer Anlage:
- Formguss zur Herstellung von Barren, Brammen oder Feingussteilen
- Schleudergussverfahren durch eine sich drehende Gießbühne mit automatischem Wuchtsystem für einen gleichbleibenden, präzisen und dynamischen Guss zur Erreichung höherer Produktkomplexität und -eigenschaften
- Geteilte Schmelz- und Gießkammern für einen einfachen Zugang für den Austausch von Tiegel und Gießeinrichtung sowie für Wartung und Reinigung
- Einfacher Be- und Entladung der Elektrode
- Möglichkeit des Multigussverfahrens mit bis zu 6 Güssen pro Elektrode ermöglicht eine hohe Produktivität mit niedrigen Betriebskosten
- Vollautomatischer Tiegelkipp-/Gießprozess und programmierbare Gießkurve
- Ganzheitliches Prozess- und Produktionsmanagementsystem (IMAS)
Aufgrund der erforderlichen manuellen Arbeit stellt der Zusammenbau der Presslinge in einer typischen Titanschwamm-VAR-Produktionslinie einen gewissen Engpass hinsichtlich der Produktivität dar. INTECO hat daher eine automatisierte Zusammenbaustation entwickelt, die in der Lage ist, die Montage von Presslingen mit 120° bzw. 180° Split-Geometrie automatisiert durchzuführen. Neben der Produktivitätssteigerung kann so auch der Faktor Mensch eliminiert werden, was zusätzlich zur Qualitätssicherung beiträgt.
Die Elektrodenzusammenbaustation (EAS) kann direkt in der Produktionsroute hinter der Kompaktierpresse und vor der Elektrodenschweißanlage (Plasma- oder Elektronenstrahl) integriert werden. Die Presslinge können über ein Schrägförderband von der Kompaktierpresse zur Zuführungseinrichtung der EAS transportiert werden. Die Zykluszeit für die Zuführung der Presslinge wird so angepasst, dass die Presslinge während der Phase des Zusammenbaus schneller und während der Ladephase der Elektrodenschweißanlage langsamer zugeführt werden.
Unsere Technologie – Ihr Vorteil
- Steigerung der Produktivität
- Sicherung der Qualität
Digitalisierung und Smart Production sind die treibenden Kräfte für Entwicklung und Veränderung in der Stahlbranche. Bei INTECO bieten wir Ihnen nicht nur erstklassiges Engineering im Anlagenbau, sondern auch maßgeschneiderte digitale Lösungen, die den anspruchsvollen Anforderungen unserer Kunden gerecht werden. Überwachen Sie Ihre Produktion effizienter und nutzen Sie die gesammelten Informationen für Anpassungen und Fortschritt.
INTECO’s Remelting Controller (IREC) is ideal to upgrade any compatible furnace with INTECOs advanced melting control algorithms. Our advanced non-linear controllers provide voltage, current, melt rate and immersion depth control. The flexible design supports all different types of power supplies such as transformers, saturable reactors, and different kinds of power supply units. Integration into complete automation systems is possible via commercially available common fieldbus technologies. The sophisticated deviation tracking warns in case there might be any defects during remelting. It can be easily expanded with IMAS essentials.
The cost-optimized charge mix calculation and optimization tool calculates the exact and cost-optimized material mix and quantity to achieve the target composition. The calculation can be based on previously prepared materials, on strategic material storage, or a combination of both, optimizing material handling by using broken lots. Micro-dosing units and segregation optimization for heavy elements can also be implemented. The tool supports compacting by considering fractional sizes, ensuring perfect physical compacting. Both, ingot and slab-based, as well as batch-based optimization are possible.
Projekte
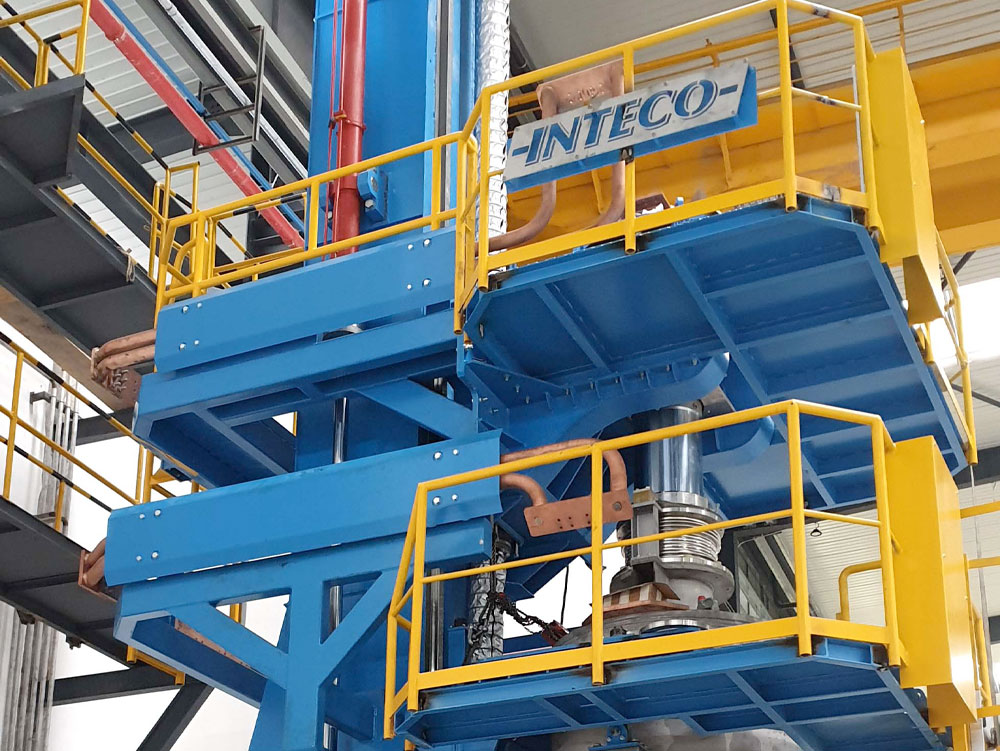
Chongqing Kingsley Titanium Technology
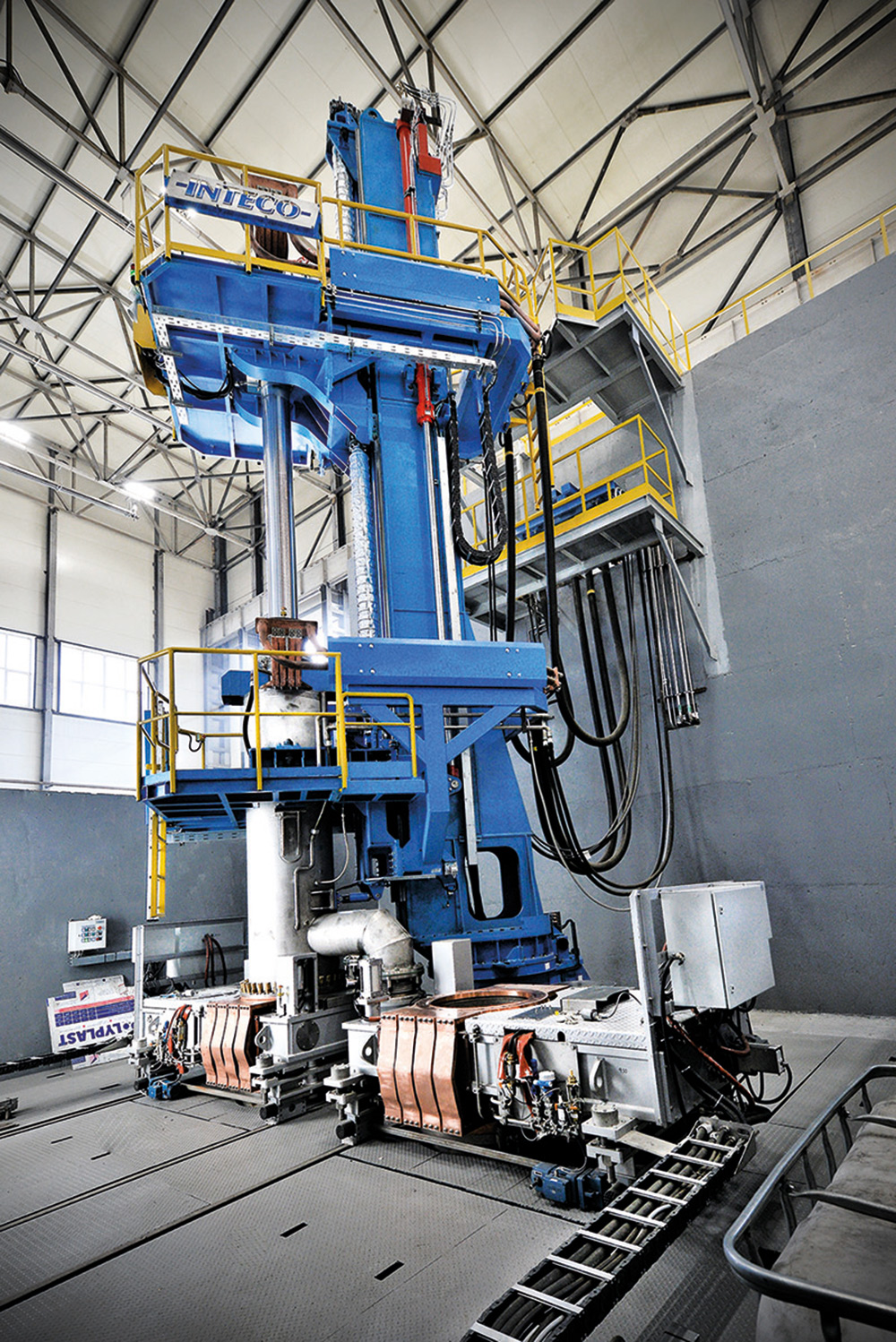
Ruspolymet
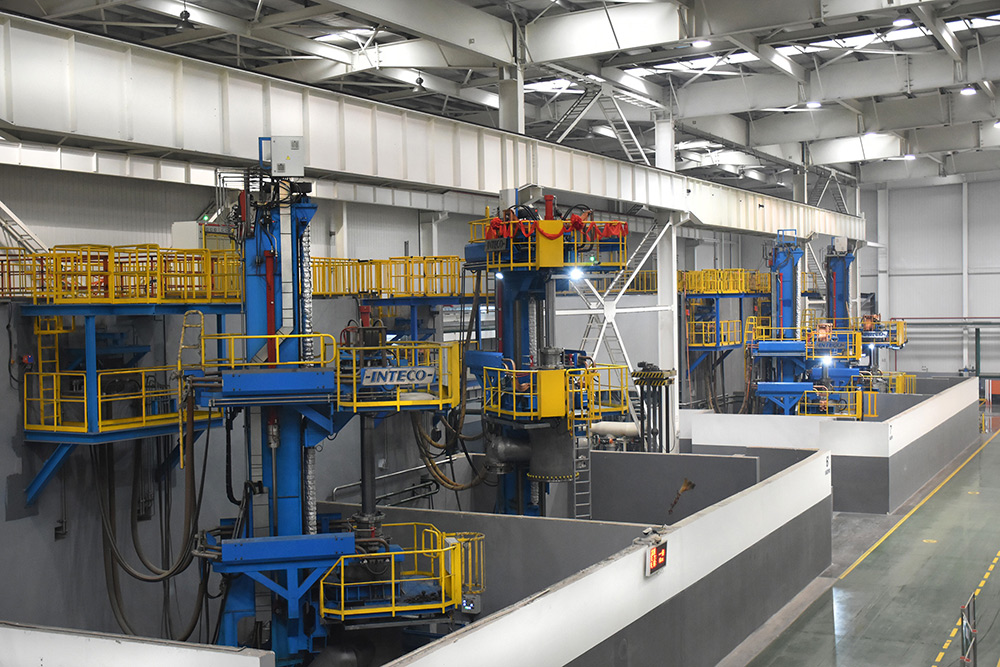
Shaanxi TianCheng Aerospace (TCAE)
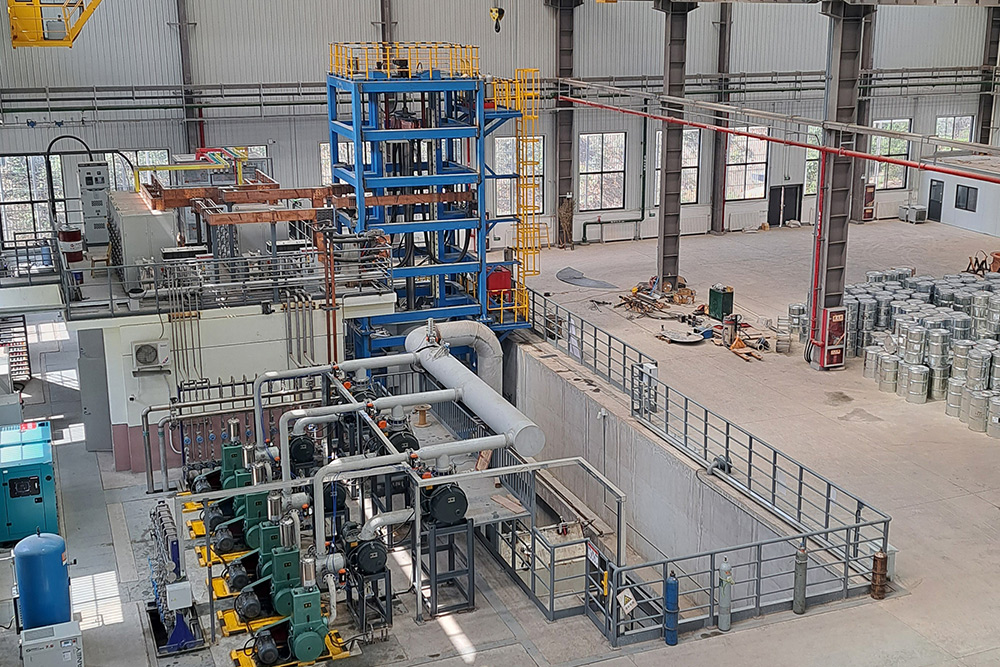
Baoji Titanium Industry
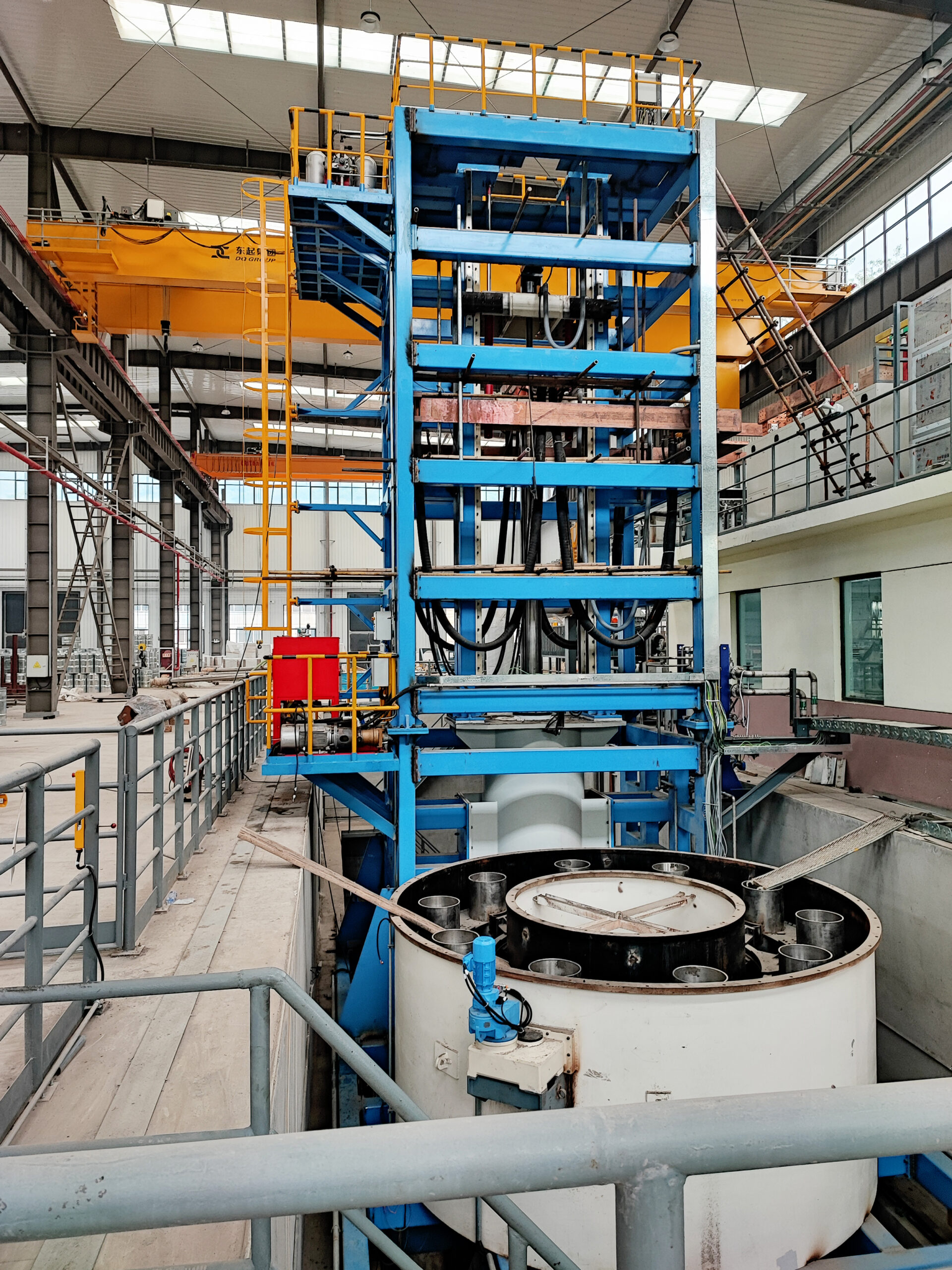