VACUUM ARC REMELTING
- General Information
- Variations
- Our technology – your advantage
- Digitalization
The strict quality requirements in the air and space industry calls for a metallurgical refining process that enhances the product quality to the highest level. The vacuum arc remelting (VAR) process has been developed in the 1950‘s with the aim of satisfying these increased demands on certain material properties of the final product. Today, the VAR process is used to significantly improve the material properties of various steels and superalloys. Because the VAR process is carried out under inert conditions (i.e. vacuum) and with controlled solidification conditions, the remelted ingot is of superior cleanliness and lowest residual gas content.
Based on INTECO‘s long-term experience and know how in the field of vacuum metallurgy as well as sophisticated control systems for remelting systems, a wide range of well-proven and specialized solutions in VAR technology can be offered to our customers meeting the highest standards.
- VAR for steels, super alloys and reactive materials
- From lab-scale to 30t ingot weight and more
- Partial pressure remelting for minimization of evaporation losses
- Helium cooling system for improved heat transfer between mould wall and ingot
- XY adjustment for precise electrode alignment
- Patented combined ESR/VAR concept
- Coaxial furnace design with defined current path for highest reproducibility
- Sophisticated drip short analysis functionality (IDRIP®)
- Horizontal XY adjustment of the electrode in the crucible for maintaining a constant gap
- Optimized weighing system for accurate control of the remelting parameter
- Tailor-made ergonomic design according to customer specific requirements
- best accessibility and easy maintenance
- Comprehensive process simulation model developed with the University of Leoben
- Holistic process and production management system (IMAS) for overall recipe management, data storage and definition of key performance parameters
Digitalization and smart production are transforming the steel industry, driving development and change. At INTECO, we offer not only first-class engineering in plant construction, but also customized digital solutions tailored to our customers’ demands. Enhance your production with our digital solutions and utilize the collected data to make strategic adjustments and drive continuous progress.
INTECO’s Remelting Controller (IREC) is ideal to upgrade any compatible furnace with INTECOs advanced melting control algorithms. Our advanced non-linear controllers provide voltage, current, melt rate and immersion depth control. The flexible design supports all different types of power supplies such as transformers, saturable reactors, and different kinds of power supply units. Integration into complete automation systems is possible via commercially available common fieldbus technologies. The sophisticated deviation tracking warns in case there might be any defects during remelting. It can be easily expanded with IMAS essentials.
The IMAS Production Management (IMAS-PM) manages conventional functions of a production management system such as recipe management, order scheduling, downtime recording as well as equipment and consumable consumption. Nevertheless, the main focus is on quality assurance. The integrated check-list module provides an aviation industry compliant solution for tracking every production step, not only in a generic way, but tailored to individual needs. You have the choice between a traditional, paper driven concept, an electronical, tablet-based application, or a combination of both. The production-based review system provides summary reports and detailed ingot or batch analysis for all relevant product categories such as ingots, slabs, powder, or flakes. The system includes rule-based deviation control modules and ensures that only high-quality products are being shipped. Technically, the system can be implemented into any existing production setup with a PLC-friendly standard interface such as OPC-UA and standardized REST interface for higher-level applications like ERP systems.
IMAS essentials are the perfect add-ons for single remelting units. The user-friendly web-based interface provides master data management for mould and electrode formats in multiple languages. The template-based melting recipe system facilitates standardization and aims for constant quality improvement. Detailed production reports, generated for each melting operation, include production key performance indicators and documentation of quality-related incidents. Information on the ingot position where the incident occurred, is calculated. The high-resolution trend tool allows in-depth analysis. All relevant data points are recorded in PLC cycle time and stored in a head-based structure. Time-synced available video streams from furnace cameras facilitate in matching visual inspection with process values.
INTECO’s Drip Short Measuring (IDRIP) device is based on an embedded controller and integrates easily into existing automation systems such as PROFIBUS or PROFINET. It features a web-based interface for diagnosis and configuration and a parallel voltage measuring device provides a sampling rate of 200kHz. If the input voltage falls below a defined trigger level, it triggers a single drip. These drips are categorized by the duration of the drip to provide a statistical analysis. Its small size allows easy installation in existing plants.
Projects
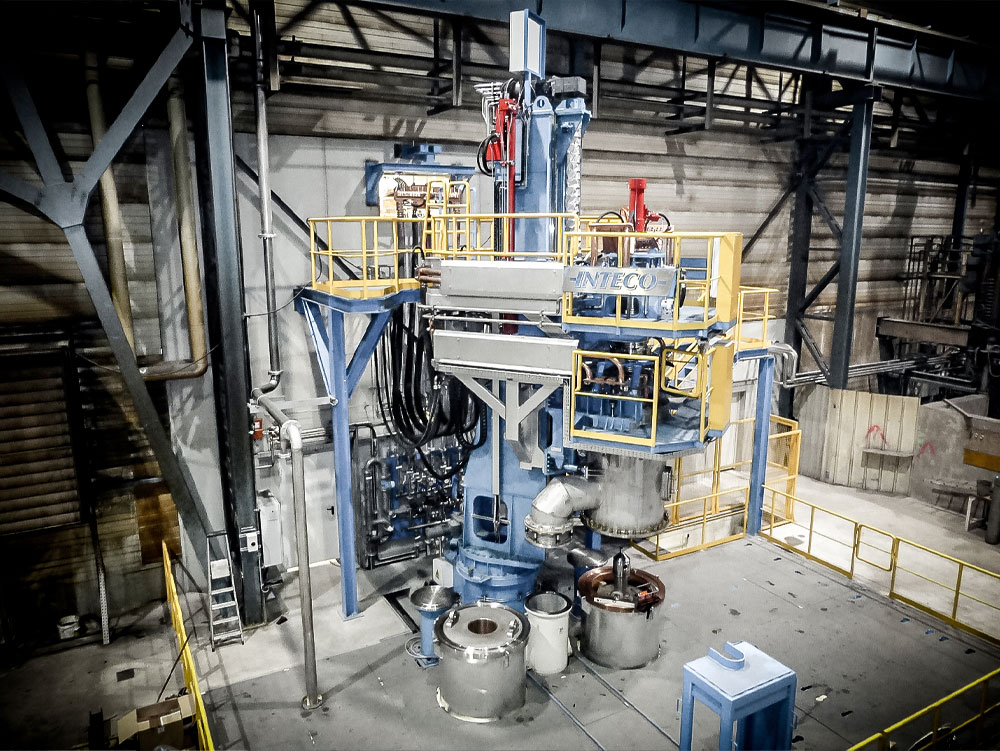
BGH Lippendorf
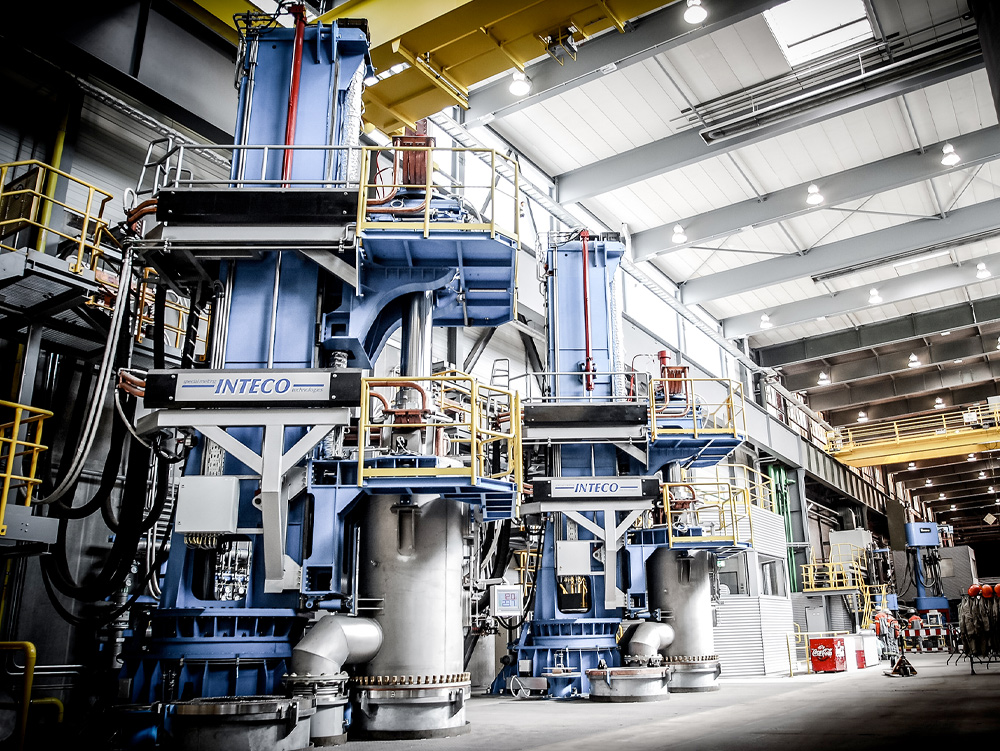
Deutsche Edelstahlwerke

Ruspolymet
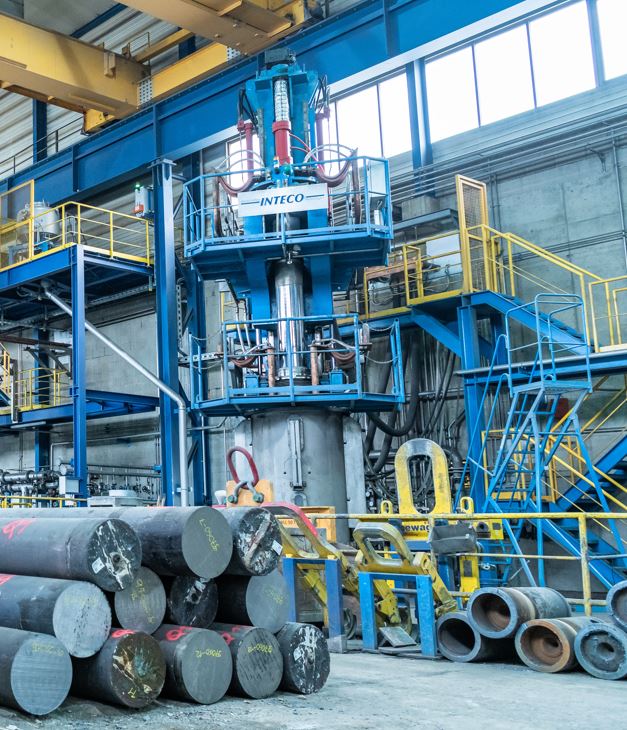
Breitenfeld Edelstahl
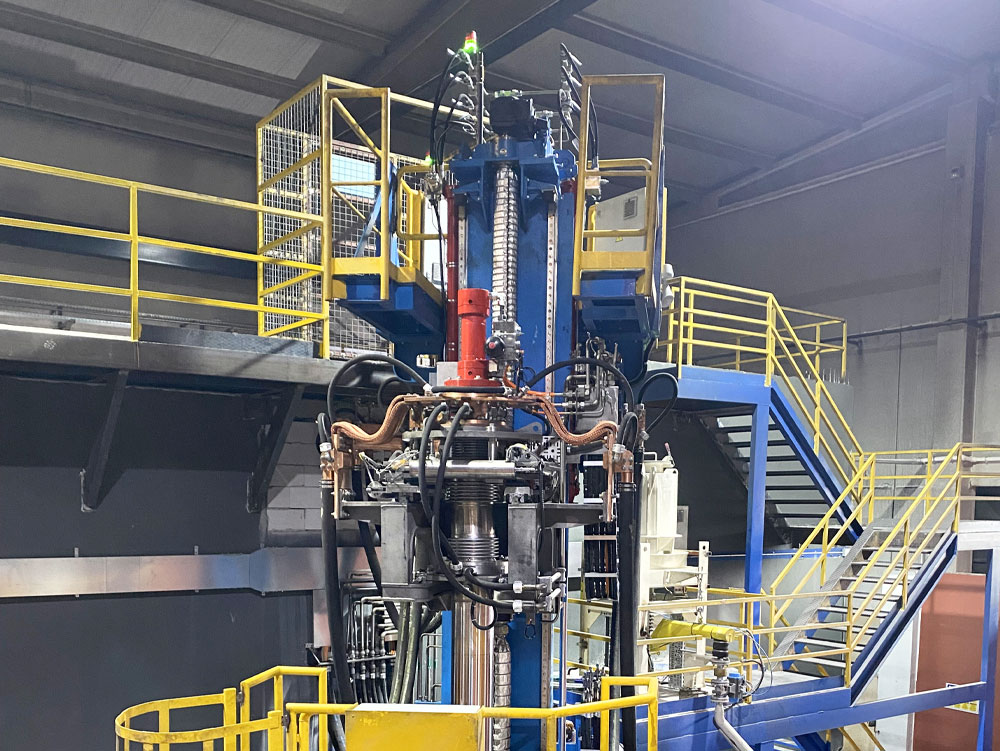