TITANIUM PRODUCTION
- General Information
- Vacuum Arc Remelting of Titanium
- Vacuum Arc Cold Hearth Skull Melting
- Electrode Assembly Station
- Digitalization
Since the 1950s, titanium has been used primarily in the aerospace industry thanks to its exceptional properties. Today, about 80% of titanium is used by the aerospace industry and 20% by non-aerospace industries such as metal finishing, chemical processing, consumer products and medical implants. The conversion of purified titanium sponge into commercially pure titanium or titanium alloys involves several processes which can nowadays be realized via two independent production routes.
In the titanium sponge VAR production route, titanium sponge is mixed with various alloy additives. This mixture is then pressed into compacts and welded together in a vacuum plasma welding process forming a sponge electrode, which is then remelted up to three times in a vacuum arc remelting process, depending on specifications. The technically acceptable titanium ingot must then be suitable for subsequent further processing using forging and rolling processes to produce rolled products such as bars, billets, wires, tubes, plates and sheets.
In addition to the classic titanium sponge VAR production route, the cold hearth remelting route is applied by direct melting, refining and casting of raw materials such as scrap, sponge and alloying elements into titanium ingots and slabs. In this process, the individual raw materials are fed continuously or in batches into a cold hearth remelting furnace, where they are melted by a high-energy source (electron beam or electric arc). After casting and solidification, the produced ingots can either be remelted again in a vacuum arc remelting process or further processed conventionally by forging or rolling, depending on requirements.
As a premium supplier for the titanium industry with about 20 years of experience, we offer a broad portfolio of different technologies and systems tailored to specific demands. Starting from a feasibility and pre-investment study to define the process route and provide necessary CAPEX and OPEX evaluations followed by the supply of equipment, INTECO can act as a technology partner and even support the customer in product certification such as needed for the aerospace industry. The whole package is rounded off by providing the complete know-how for the various titanium production routes. Furthermore, INTECO has developed a sophisticated production management system (IMAS) covering the entire process route including pre-defined procedures and ultimately an operator independent and repeatable process, already complying with the requirements of industry 4.0.
Vacuum arc remelting of titanium is a core technology for producing commercially pure and alloyed titanium with high demand on purity and quality. The remelting of titanium, in principle, is very similar to the VAR remelting of steel and superalloys but with different aspects in terms of process control and safety measures.
Based on INTECO´s long-lasting experience in the field of vacuum arc remelting, INTECO has developed a new and innovative furnace concept for titanium remelting which features all state-of the art characteristics. Furthermore, a comprehensive process simulation model has been exclusively developed with the Montanuniversity of Leoben to provide further insights into this complex remelting process allowing our customers to enhance their process know how and optimize their entire production.
Our Technology – Your Advantage
- State-of-the-art arc centralization system for homogeneous distribution of the magnetic field from the bottom to the top for highest safety and improved metallurgical performance
- High productivity thanks to vacuum tight lock valves above the melt station
- Comprehensive process simulation model exclusively developed with the Montanuniversity of Leoben
- Holistic process and production management system (IMAS) for overall data management, data storage and definition of key performance parameters
Given the current challenges on the titanium and raw materials market and the global aim of reducing CO2 emissions, there is a growing trend among titanium producers worldwide to increase recycling rates and flexibility in their production processes. To meet these new challenges, INTECO has rehought and revolutionized the existing and proven vacuum arc skull melting process.
In addition to the conventional process, in which an electrode is melted in a water-cooled copper crucible and the melt is then poured into a casting mould, this new system also makes it possible to batch larger quantities of scrap into the copper crucible between casting cycles. This technology therefore makes it possible to recycle up to 100% of the titanium scrap used.
Homogenization as well as refining the melt from refractories and impurities is obtained by a long soaking time of the liquid metal. Heavy particles sink down and remain in the solidified skull, which remains in the copper crucible after casting.
In order to ensure highest possible flexibility, two different casting techniques were combined in one plant: Static casting for ingots and slabs and dynamic casting (centrifugal casting technique) for investment cast parts.
Our Technology – Your Advantage
- Possibility to use a double round cold skull crucible (oval shape) for increased metallurgical efficiency and cast weight flexibility > 1000 kg drum feeder to feed raw material or different alloy materials into the copper crucible during the process for recycling rates of titanium scrap of up to 100%
- Two casting techniques are combined in one plant
- Static casting for producing ingots, slabs or investment cast parts
- A rotational cast table with auto balancing system with high balancing accuracy for dynamic casting can be used for centrifugal casting technique to achieve advanced product complexity and properties
- Split melt and casting chamber design allowing easy access for crucible and casting setup exchange as well as maintenance and cleaning
- Easy loading and unloading process of electrode
- Possibility of a multicast for up to 6 casts per electrode allows high productivity with low operating costs
- Fully automated crucible tilting/pouring process and programmable pouring speed
- Ganzheitliches Prozess- und Produktionsmanagementsystem (IMAS)
- Holistic process and production management system (IMAS)
As a result of the manual labor required, the assembly of the compacts in a typical titanium sponge VAR production route represents a certain bottleneck in terms of productivity. INTECO has therefore developed an automated assembly station that is able to automatically carry out the assembly of compacts with 120° or 180° split geometry. In addition to increasing productivity, the manpower factor can also be eliminated, which also contributes to quality assurance.
The electrode assembly station (EAS) can be integrated directly into the production route downstream of the compacting press and upstream of the electrode welding system (plasma or electron beam). The compacts can be transported from the press to the feeding device of the EAS via an inclined conveyor belt. The cycle time for feeding the compacts is adjusted so that the compacts are fed faster during the assembly phase and slower during the charging phase of the electrode welding system.
Our Technology – Your Advantage
- Enhanced productivity
- Highest quality guaranteed
Digitalization and smart production are transforming the steel industry, driving development and change. At INTECO, we offer not only first-class engineering in plant construction, but also customized digital solutions tailored to our customers’ demands. Enhance your production with our digital solutions and utilize the collected data to make strategic adjustments and drive continuous progress.
INTECO’s Remelting Controller (IREC) is ideal to upgrade any compatible furnace with INTECOs advanced melting control algorithms. Our advanced non-linear controllers provide voltage, current, melt rate and immersion depth control. The flexible design supports all different types of power supplies such as transformers, saturable reactors, and different kinds of power supply units. Integration into complete automation systems is possible via commercially available common fieldbus technologies. The sophisticated deviation tracking warns in case there might be any defects during remelting. It can be easily expanded with IMAS essentials.
The cost-optimized charge mix calculation and optimization tool calculates the exact and cost-optimized material mix and quantity to achieve the target composition. The calculation can be based on previously prepared materials, on strategic material storage, or a combination of both, optimizing material handling by using broken lots. Micro-dosing units and segregation optimization for heavy elements can also be implemented. The tool supports compacting by considering fractional sizes, ensuring perfect physical compacting. Both, ingot and slab-based, as well as batch-based optimization are possible.
Projects
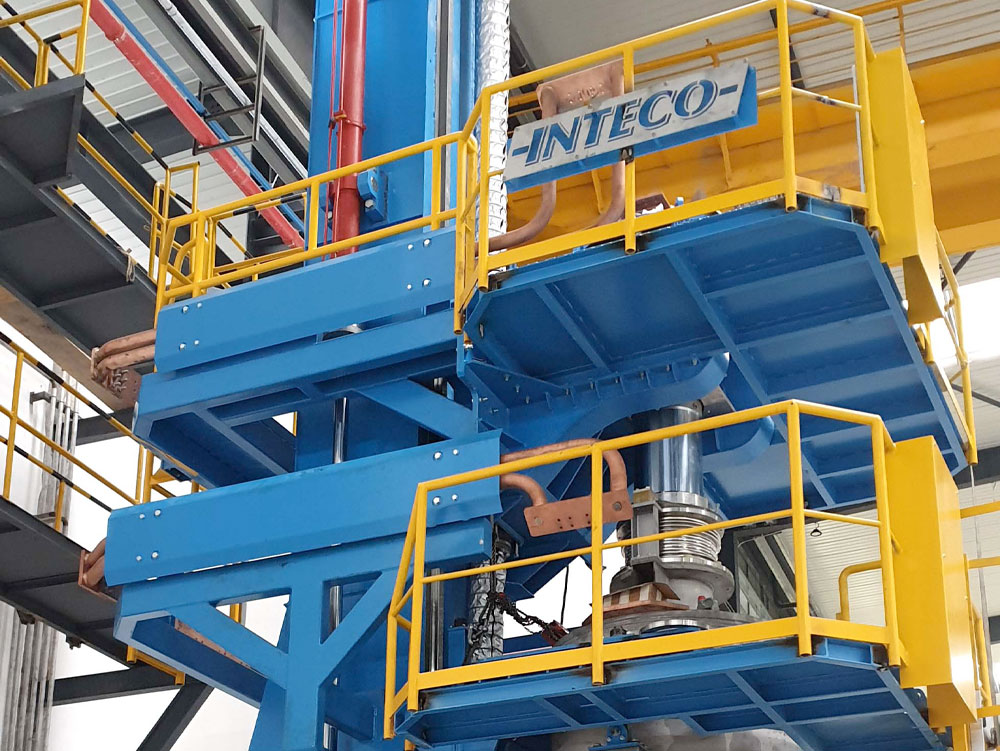
Chongqing Kingsley Titanium Technology
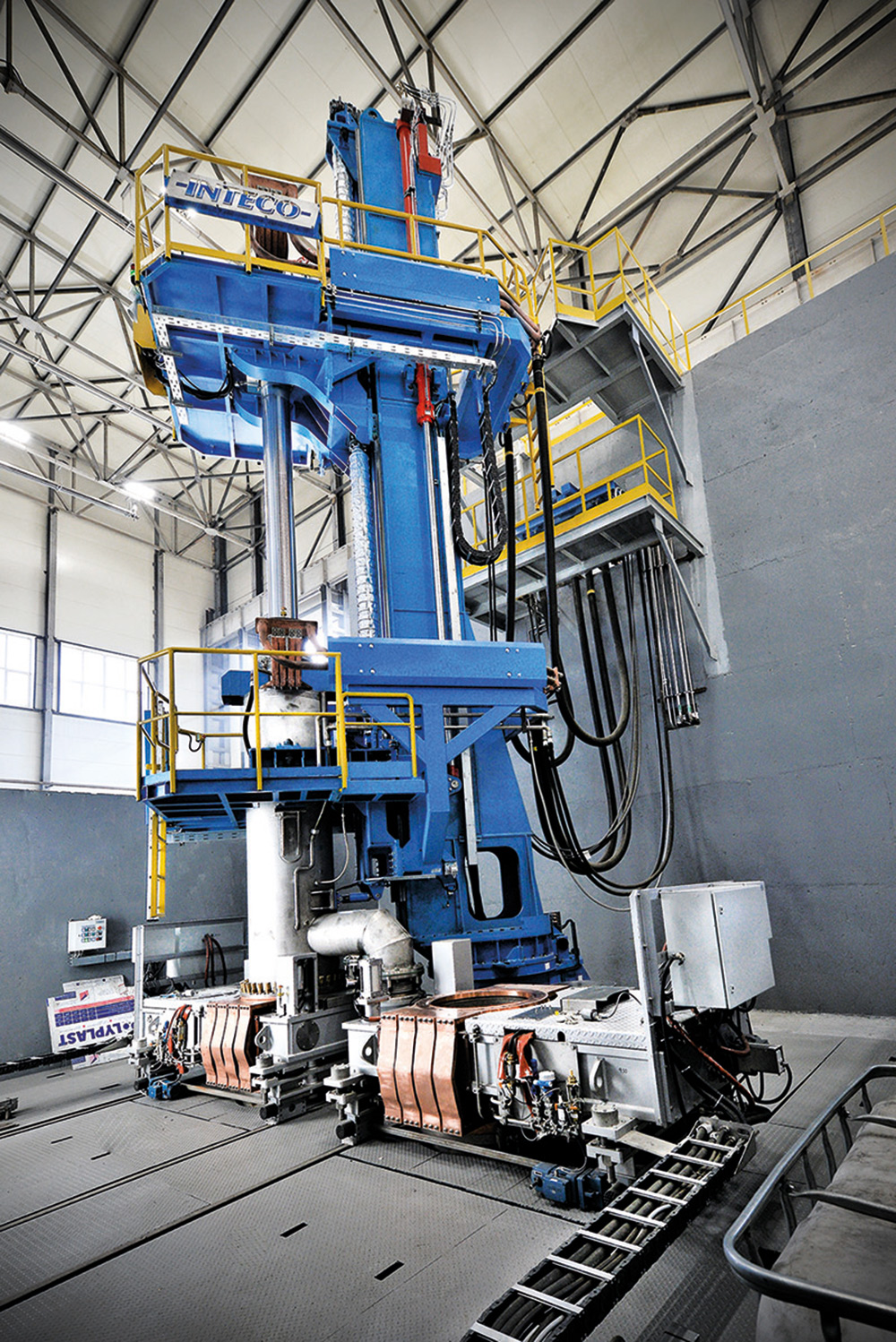
Ruspolymet
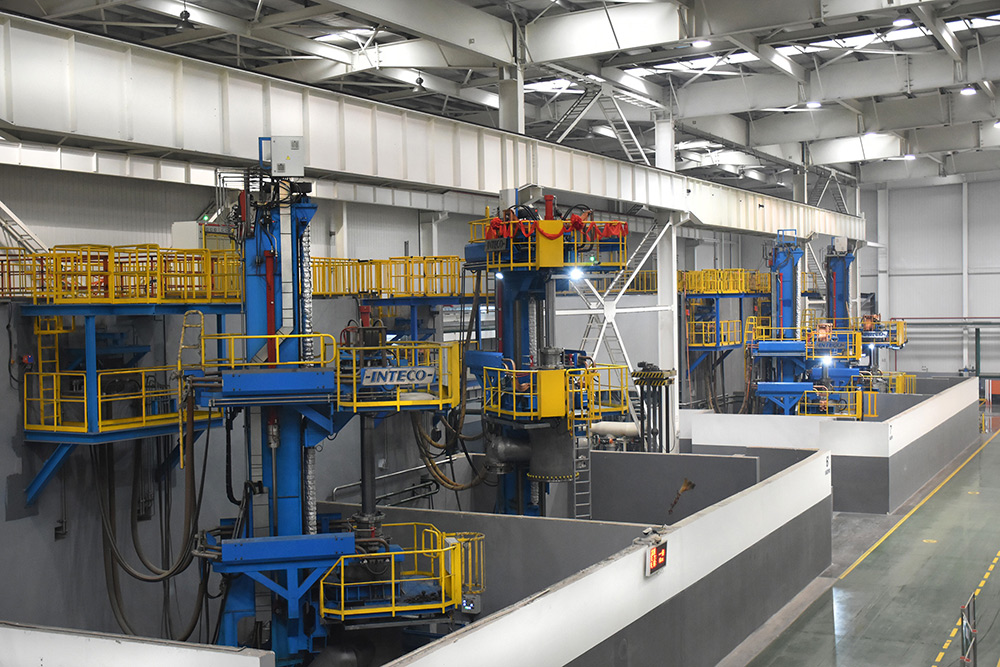
Shaanxi TianCheng Aerospace (TCAE)
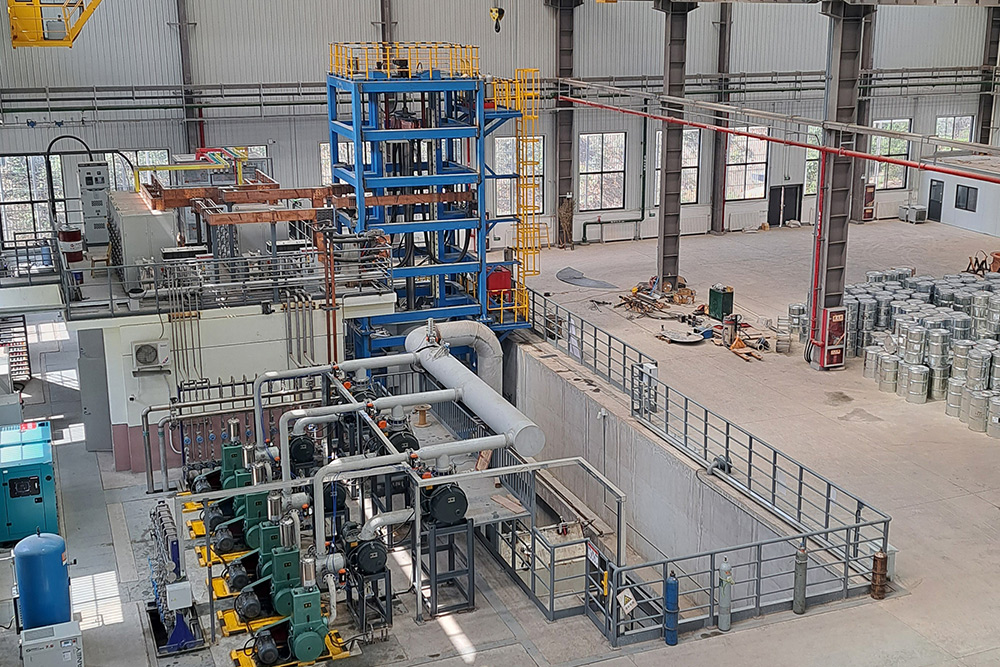
Baoji Titanium Industry
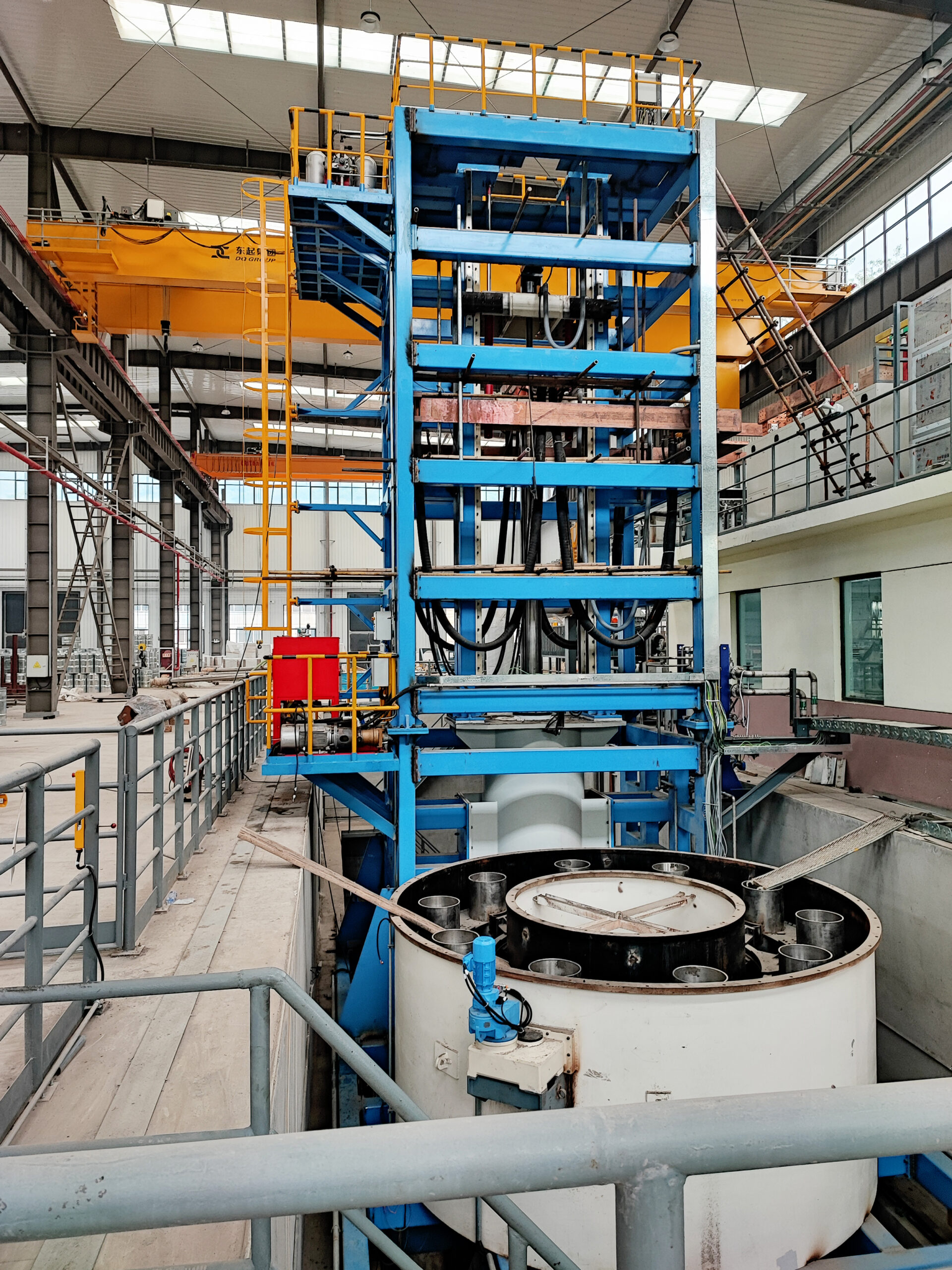