RH VACUUM DEGASSING
- General information
- Variations
- Our technology – your advantage
- Digitalization
Since the introduction of Ruhrstahl-Heraeus (RH) degassing technology in the late 1950s, the RH degassing process has become an important tool in modern steel plants. It originally was used to adjust low hydrogen contents in liquid steel. Over the past decades, the process has been adapted to the needs of today’s steel producers through continuous development and improvement. Today, this technology is mainly used to produce LC (low carbon) and ULC (ultra low carbon) steels and to minimize the hydrogen content. The RH degassing process has proven itself particularly well suited for operations requiring short tap-to-tap times and treatment sizes of up to 400t.
In general, the RH process offers the following advantages:
- Utilisation of cheaper materials with high carbon content
- Reduction of production costs
- Improved product quality due to low gas content
- Ability to produce ELC qualities with minimum chromium loss
- Achievability of strict analysis tolerances
- High chromium yield
- Single or twin operation stand
- RH-vessel fast exchange system
- Steam ejector vacuum pumps and ry mechanical vacuum pumps
- Variable ladle / vessel lifting systems
- Top-burner & O2-blowing lance system
- Variable dust separating / cooling system
Digitalization and smart production are transforming the steel industry, driving development and change. At INTECO, we offer not only first-class engineering in plant construction, but also customized digital solutions tailored to our customers’ demands. Enhance your production with our digital solutions and utilize the collected data to make strategic adjustments and drive continuous progress.
The smart process camera is a retractable and therefore well protected optical system that directly streams a high-resolution video to the control room to ensure safe low-manpower operation. The optional thermal imaging variant provides a clear view through smoke and dust and serves for automatic stirring adjustment. Additional generated process information such as slag height and stirring eye detection enhances metallurgical model accuracy and safety.
The IPAS off-gas measuring for RH applications includes a gas extraction system, an off-gas analyzer, and a flow measurement device. The off-gas analyzer measures CO and CO2 through an infrared photometer, H2 through thermal conductivity and O2 through electromagnetic force measurement. The flow meter uses ultrasound measurements or hot-wire anemometer with temperature and pressure data for normalization to standard cubic meters per hour. The self-calibrating IPAS system combined with online process models, provides hybrid decarburization and degassing modelling.
INTECO’s Material Handling System Automation offers precise and time-critical alloying for all secondary metallurgy plants. Its recipe-based approach serves various technologies such as positive and negative weighing, shuttles, weighing bands, or hoppers and integrates micro-dosing systems and wire feeding machines. Moreover, it provides fallback modes for redundant feeding lines as well as sequential dosing of materials or material groups to add slag builders and alloys in the correct order.
The thermochemical model calculates oxide and element activities based on current process conditions and events, current heat state and energy losses and gains. In this context, IMAS modeling includes a thermophysical property library, reaction enthalpies, coefficients for interactions providing the necessary parameters, and coefficients to determine and calculate the activities.
The temperature model accounts for the temperature losses due to radiation and convection as well as the changes in temperature due to purging, material addition and heating. Temperature changes due to reactions are also taken into account and are therefore coupled with the basic thermochemical model. Both are not only used to calculate the actual heat state but also to predict take-over time and temperature.
The oxygen model calculates the required amount of oxygen to achieve target decarburization, considering initial steel samples and current temperature that lead to a physically based oxygen quantity. It uses the basics of the thermochemical and thermodynamic approach and once the vacuum and/or oxygen blowing has started, the decarburization model tracks the oxidation of the elements involved. The chemical composition is updated through close interaction with the thermochemical model.
The decarburization model reacts to the oxygen injection rate and oxidizes the steel according to the thermodynamic evaluations. The decarburization model constantly checks stoichiometric oxidation against kinetic reactions and the temperature gain is back-looped to the temperature model. The degassing model calculates the removal of hydrogen and nitrogen.
IMAS-PA-RH provides advanced top-down process guidance through dynamic or static treatment planning and integrated optimization tools. Process supervision is massively improved by the cockpit view and integrated real-time process models. IMAS provides instant real-time information and alerts, based on which the operators can control and steer the process just-in-time. The heat-based data recording stores sensor data, including complex information such as video streams, allowing observation of real-time data for quality assurance and process improvement.
PROJECTS
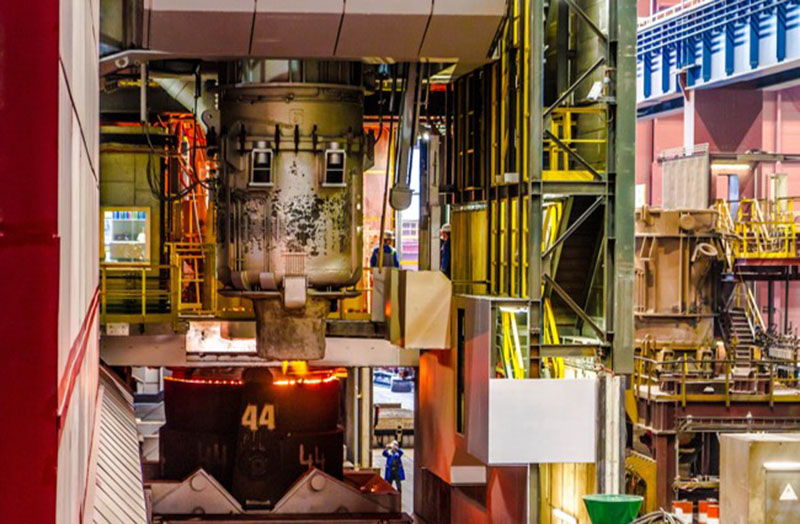
voestalpine Stahl Linz
Type: 175t RH
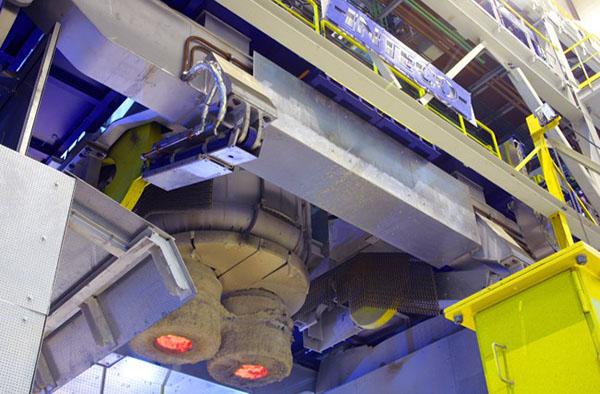
Saarstahl AG
Type: 200t RH
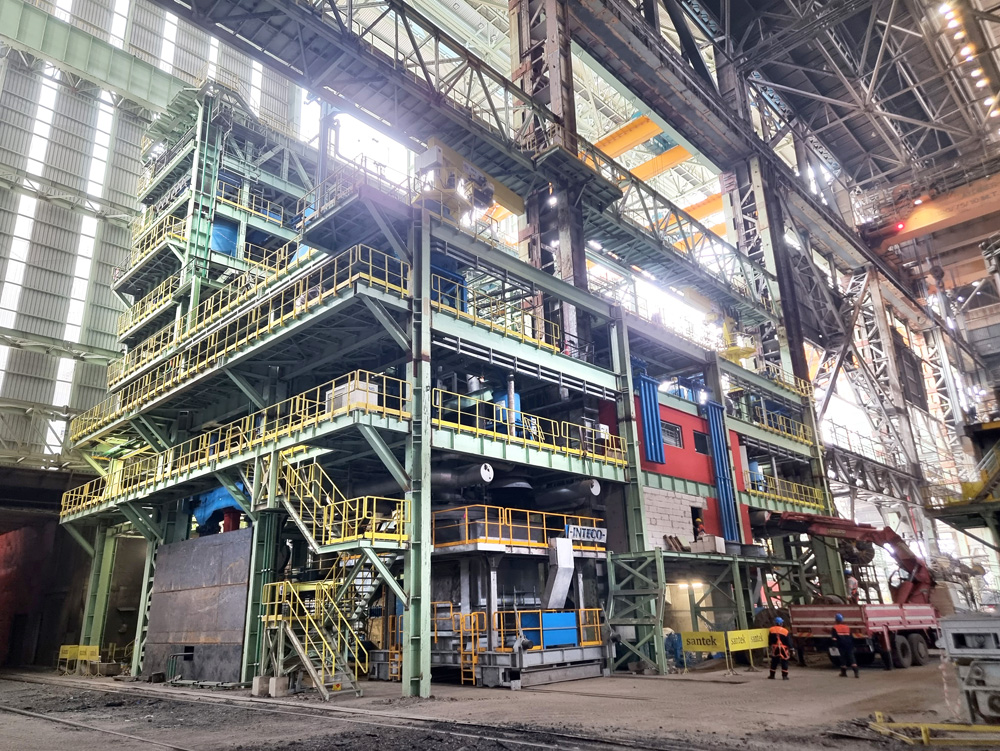
Isdemir
Type: 200t RH
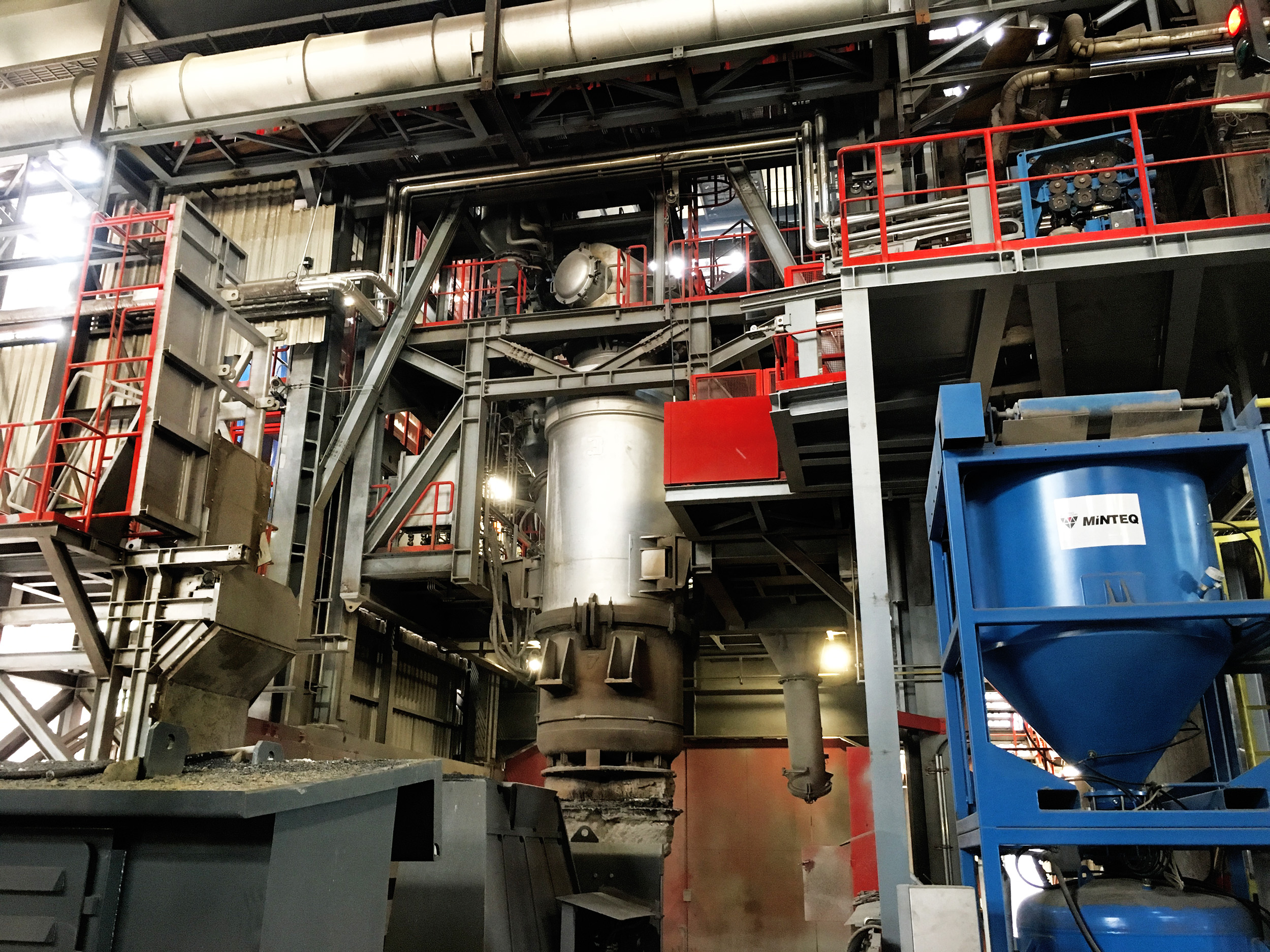
voestalpine Stahl Donawitz
Type: 67t RH
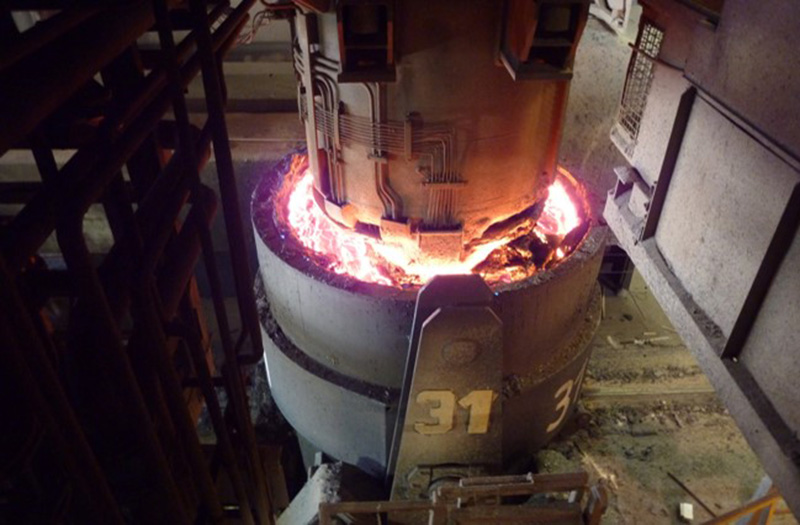
voestalpine Stahl Linz
Type: 160t RH
voestalpine Stahl Linz
Type: 175t RH
Saarstahl AG
Type: 200t RH
Isdemir
Type: 200t RH
voestalpine Stahl Donawitz
Type: 67t RH
voestalpine Stahl Linz
Type: 160t RH