INGOT CASTING
- Ingot casting
- ATS – Advanced Teeming System
- Vacuum ingot casting
- Casting car
- Digitalization
Ingot casting is a suitable process to produce all steel grades, from unalloyed and high-alloyed (e.g., tool steel) to special steels. Although continuous casting has largely replaced ingot casting, it remains the technology of choice for highly flexible special steel plants. Ingots can be manufactured in an incredible variety of shapes—rectangular, square, round, polygonal, or octagonal—ranging from 500kg to over 700t, and in all conceivable steel grades.
In the commonly used bottom pouring method, liquid steel is poured into a trumpet and directed through channel bricks to the mould, which is filled from bottom to top (upward). This method is typically applied for ingots weighing from 500kg up to approximately 200t. Specialized processes, such as INTECO’s perfected multi-ladle casting, allow secure casting of multiple ladles into a single ingot with high casting weights.
INTECO’s scope of services includes the configuration of the casting operation, mould design, provision of casting recipes, and supply of all necessary equipment, such as casting casrs and mould cleaning systems.
ATS, the Advanced Teeming System by INTECO, represents the cutting-edge solution for achieving automated, high-performance ingot casting with minimal manual involvement. INTECO’s innovative teeming system revolves around the concept of semi- to fully automated circulation and handling of casting sets. It incorporates a substantial level of automation and robotics, enhancing safety and ergonomics for operators. Key benefits include reproducible production processes and higher product yield.
Reference projects:
- Metal Ravne
- Buderus Edelstahl
- Daye Special Steel
- Gloria Materials Technology

Plate cleaning station
Bottom plate preparation
Mould preparation
Mould cleaning unit
Trumpet erection
Stripping
Hot-top cleaning
Ingot casting car
Ingot casting car
Casting station
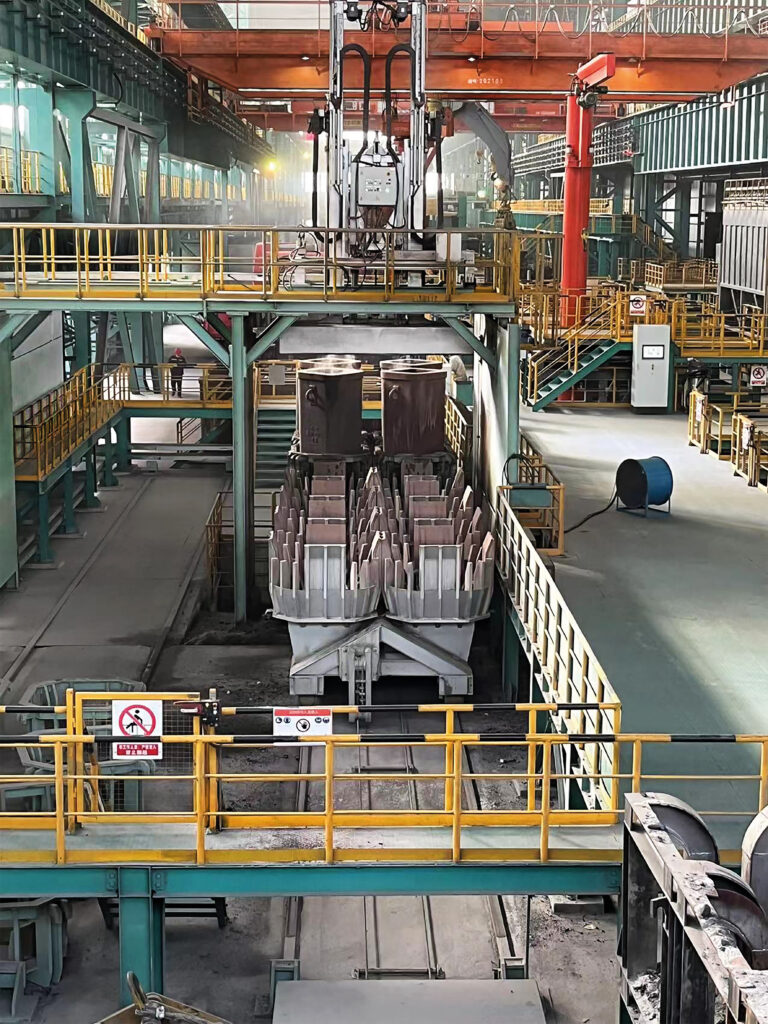
Vacuum ingot casting is the technology of choice for very large ingots. The largest systems supplied by INTECO worldwide allow production of ingots exceeding 700t.
Casting under vacuum enables attainment of the lowest hydrogen content, since there is no hydrogen absorption during casting, thus preventing flake formation.
INTECO provides customized plant solutions for all ingot weight and throughput requirements. Both conventional steam jet pumps and mechanical vacuum pumps are used as vacuum systems. In addition to engineering and delivering the plants, INTECO provides expertise in mould design, casting parameters, and more.
To produce high-quality ingots, it is nowadays considered state-of-the-art to use an ingot casting car with casting rate control and casting stream protection. The three-dimensional adjustability of the ladle in the car allows easy and perfect positioning of the ladle slide gate over the trumpet. The casting stream protection guarantees shielded casting during the whole process for increased steel quality and avoidance of re-oxidation. INTECO’s Casting Rate Controller (ICAST) in combination with an accurate weighing system is essential for pouring rate control (independent of the ferro-static pressure in the ladle) throughout the entire casting process.
Digitalization and smart production are transforming the steel industry, driving development and change. At INTECO, we offer not only first-class engineering in plant construction, but also customized digital solutions tailored to our customers’ demands. Enhance your production with our digital solutions and utilize the collected data to make strategic adjustments and drive continuous progress.
ICAST, which stands for INTECO’s Casting Rate Controller, enables automated casting with consistent pouring rates. Specially developed algorithms control the ladle slide gate and, consequently, the fully automated pouring rate for a defined casting profile with multiple process phases. ICAST can be utilized with casting cranes or INTECO’s ingot casting cars, providing the option for semi-automatic ladle positioning. ICAST is not only perfect for new installations but also an ideal solution for modernization projects, enhancing plant operation through seamless installation. A significant advantage of ICAST lies in minimizing the human factor in controlling the casting process.
IMAS-PA-IC provides advanced top-down process guidance through dynamic or static treatment planning and integrated optimization tools. Process supervision is massively improved by the cockpit view and integrated real-time process models. IMAS provides instant real-time information and alerts, based on which the operators can control and steer the process just-in-time. The heat-based data recording stores sensor data, including complex information such as video streams, allowing observation of real-time data for quality assurance and process improvement.
PROJECTS
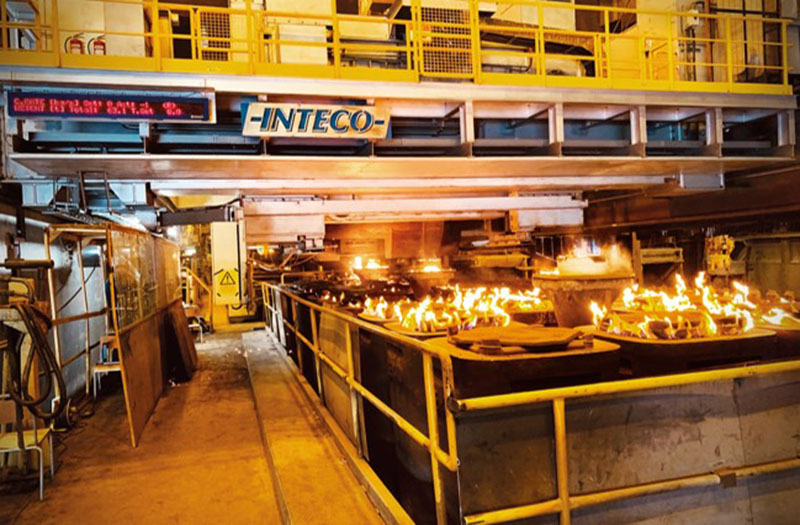
Ovako
two 100t ingot casting cars
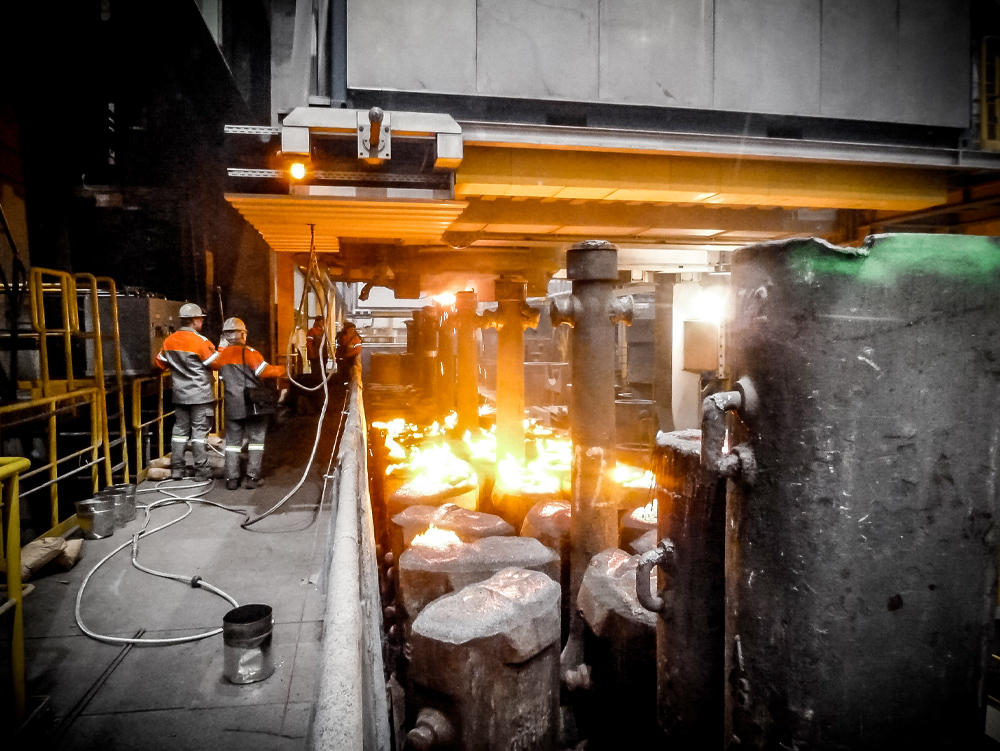
Buderus Edelstahl
Two 200t ingot casting cars & advanced Teeming System
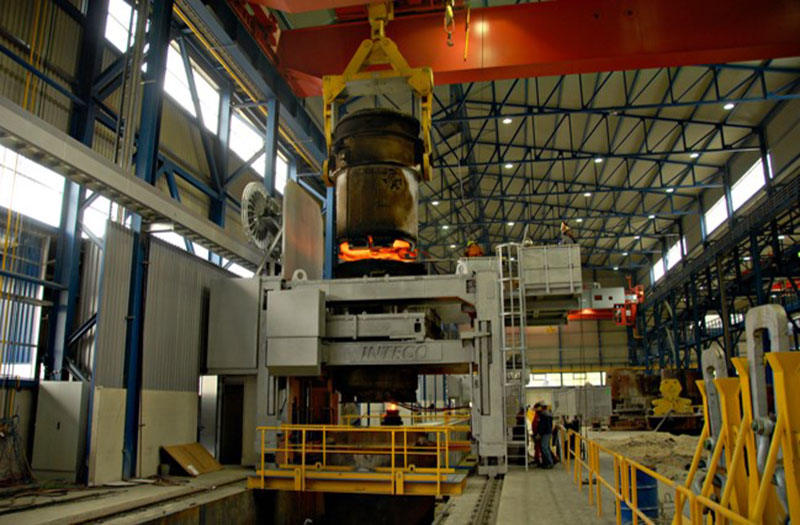
Breitenfeld Edelstahl
two 65t ingot casting cars
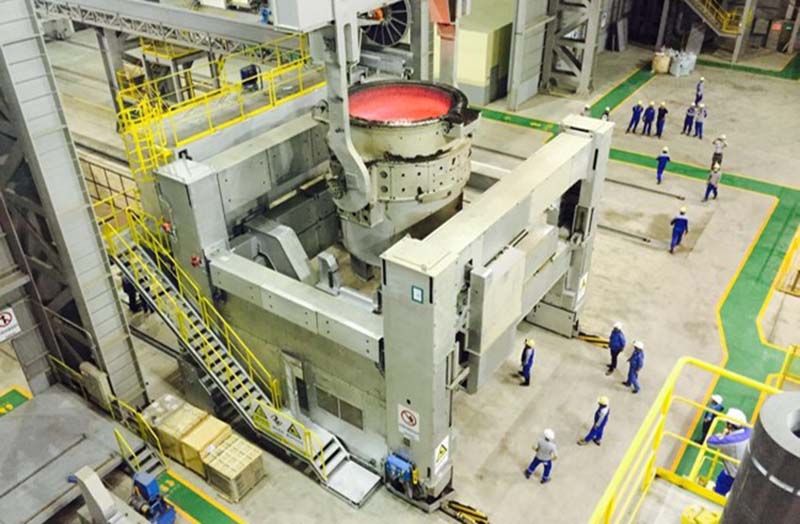
Taewoong Special Steel
700t vacuum ingot casting
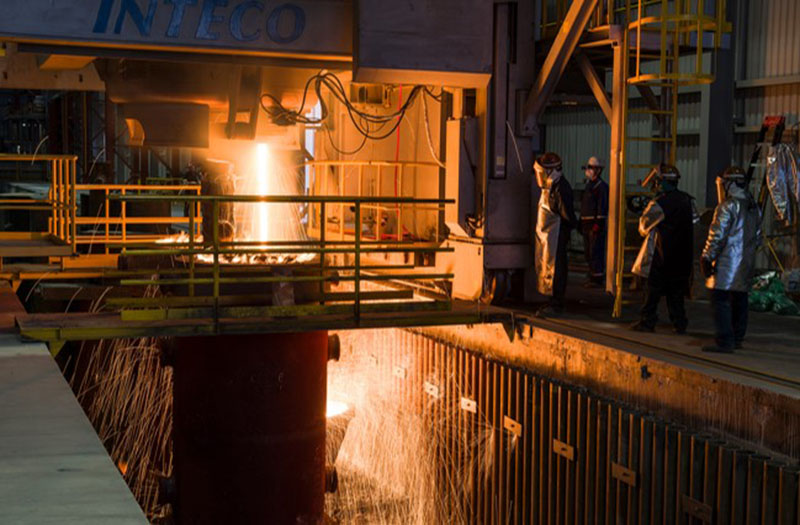
Grupo FRISA
50t ingot casting car, mould washing unit, plate transfer and tilting device
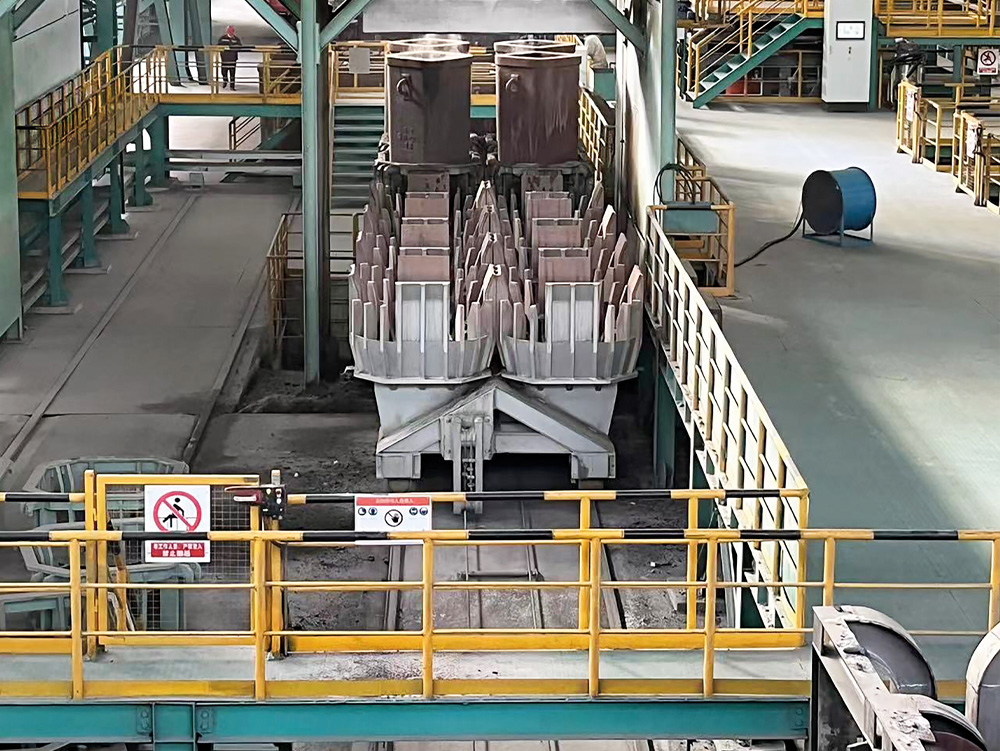
DAYE Special Steel
Ovako
two 100t ingot casting cars
Buderus Edelstahl
Two 200t ingot casting cars & advanced Teeming System
Breitenfeld Edelstahl
two 65t ingot casting cars
Taewoong Special Steel
700t vacuum ingot casting
Grupo FRISA
50t ingot casting car, mould washing unit, plate transfer and tilting device