ELECTRO SLAG REMELTING
- General information
- Variations
- Our technology – your advantage
- Digitalization
Electro slag remelting (ESR) is still one of the most important technologies in the production of steels and super alloys of highest demand for various applications. Starting from the very beginning when ESR was used only as a desulphurization step in the late sixties, the ESR process gained increased popularity for achieving superior ingot quality with respect to segregation level, cleanliness and solidification structure.
Nowadays, the ESR process has already reached industrial maturity and is used for the refinement and quality enhancement of ingots with a variety of different plant concepts. Due to the nature of the ESR process and its complexity, a lot of research and new developments has been carried out over the last decades, resulting in newly developed technologies, plant concepts and designs.
Based on INTECO‘s long term experience in electro slag remelting and our continuous focus on further developments, a wide range of remelting technologies has been developed satisfying today’s market requirements. Today, INTECO is in the position to offer tailor-made solutions with the related production technologies for all applications, meeting our customers’ expectations with respect to product quality and process stability.
- Short collar mould plants with retractable base plate
- Patented ESRR process to produce near-net-size blocks at an increased melting rate
- Static mould plants with or without electrode exchange technology
- Combined static / collar mould plants
- Pressure ESR plants (up to 40 bar)
- Labscale ESR furnace
- Large sized ESR furnaces (ingot weight up to 250t)
- Current Conductive Mould (CCM®) technology for remelting of segregation prone alloys
- Protective gas system for lowest gas consumption (N2, Ar)
- Vacuum-tight design for evacuation before starting the process
- Coaxial high current loop to achieve superior ingot quality
- Weighing system and XY-adjustment for precise control of the remelting parameters
- In-depth process know-how and highly sophisticated process control for superior product quality
- Highest yield due to optimized starting and hot topping procedures
- Comprehensive process simulation model exclusively developed with the Montanuniversity of Leoben
- All necessary auxiliary equipment (stub welding, mould cleaning, alloy and slag dosing) available from one single supplier
Digitalization and smart production are transforming the steel industry, driving development and change. At INTECO, we offer not only first-class engineering in plant construction, but also customized digital solutions tailored to our customers’ demands. Enhance your production with our digital solutions and utilize the collected data to make strategic adjustments and drive continuous progress.
INTECO’s Remelting Controller (IREC) is ideal to upgrade any compatible furnace with INTECOs advanced melting control algorithms. Our advanced non-linear controllers provide voltage, current, melt rate and immersion depth control. The flexible design supports all different types of power supplies such as transformers, saturable reactors, and different kinds of power supply units. Integration into complete automation systems is possible via commercially available common fieldbus technologies. The sophisticated deviation tracking warns in case there might be any defects during remelting. It can be easily expanded with IMAS essentials.
The IMAS Production Management (IMAS-PM) manages conventional functions of a production management system such as recipe management, order scheduling, downtime recording as well as equipment and consumable consumption. Nevertheless, the main focus is on quality assurance. The integrated check-list module provides an aviation industry compliant solution for tracking every production step, not only in a generic way, but tailored to individual needs. You have the choice between a traditional, paper driven concept, an electronical, tablet-based application, or a combination of both. The production-based review system provides summary reports and detailed ingot or batch analysis for all relevant product categories such as ingots, slabs, powder, or flakes. The system includes rule-based deviation control modules and ensures that only high-quality products are being shipped. Technically, the system can be implemented into any existing production setup with a PLC-friendly standard interface such as OPC-UA and standardized REST interface for higher-level applications like ERP systems.
IMAS essentials are the perfect add-ons for single remelting units. The user-friendly web-based interface provides master data management for mould and electrode formats in multiple languages. The template-based melting recipe system facilitates standardization and aims for constant quality improvement. Detailed production reports, generated for each melting operation, include production key performance indicators and documentation of quality-related incidents. Information on the ingot position where the incident occurred, is calculated. The high-resolution trend tool allows in-depth analysis. All relevant data points are recorded in PLC cycle time and stored in a head-based structure. Time-synced available video streams from furnace cameras facilitate in matching visual inspection with process values.
PROJECTS

Uddeholms AB
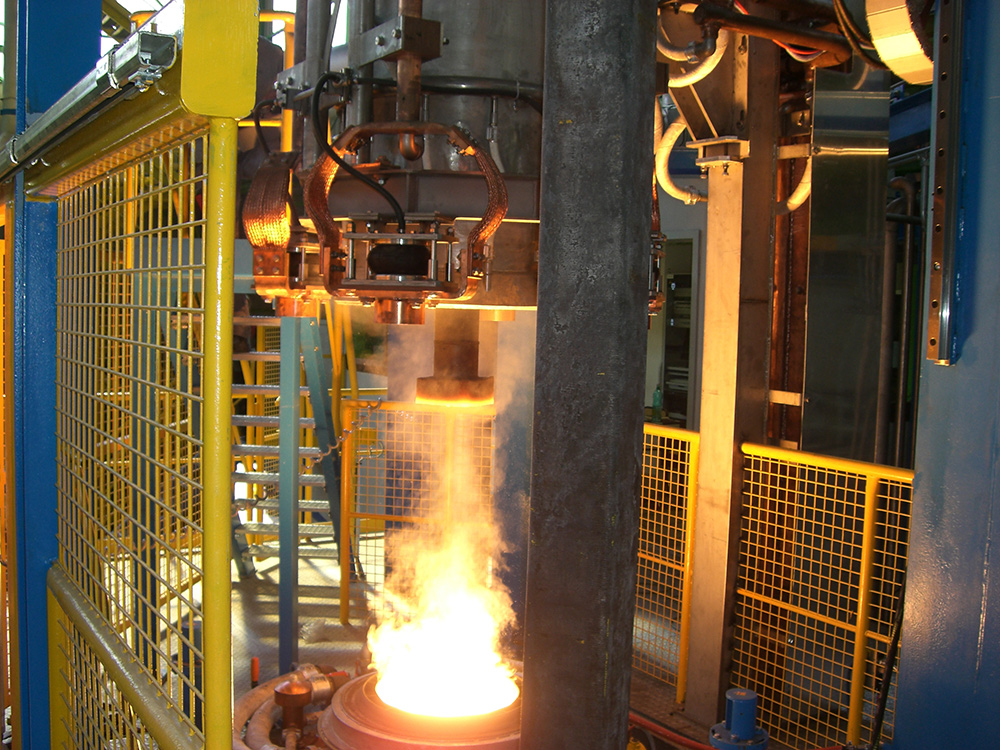
Ugitech
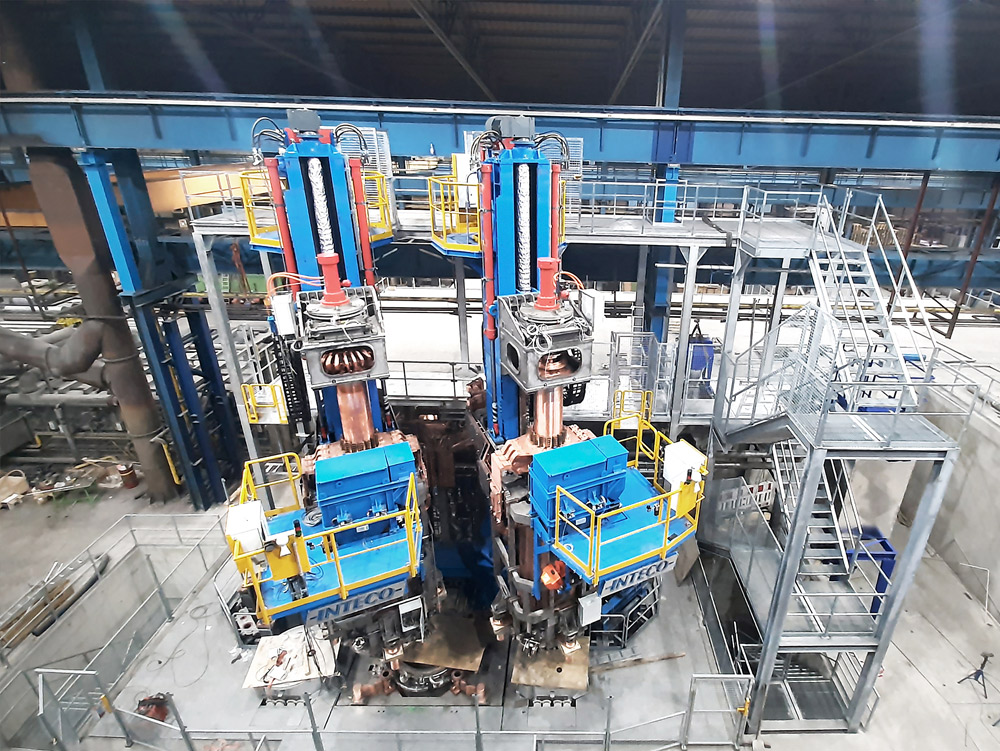
BGH Lippendorf
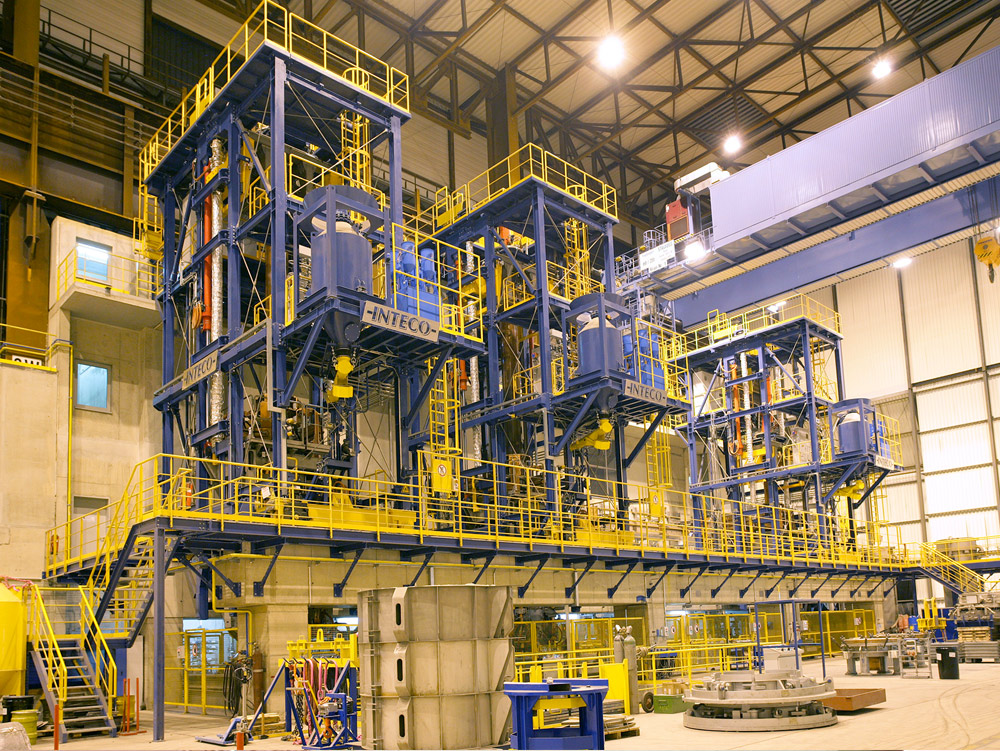
Saarstahl AG
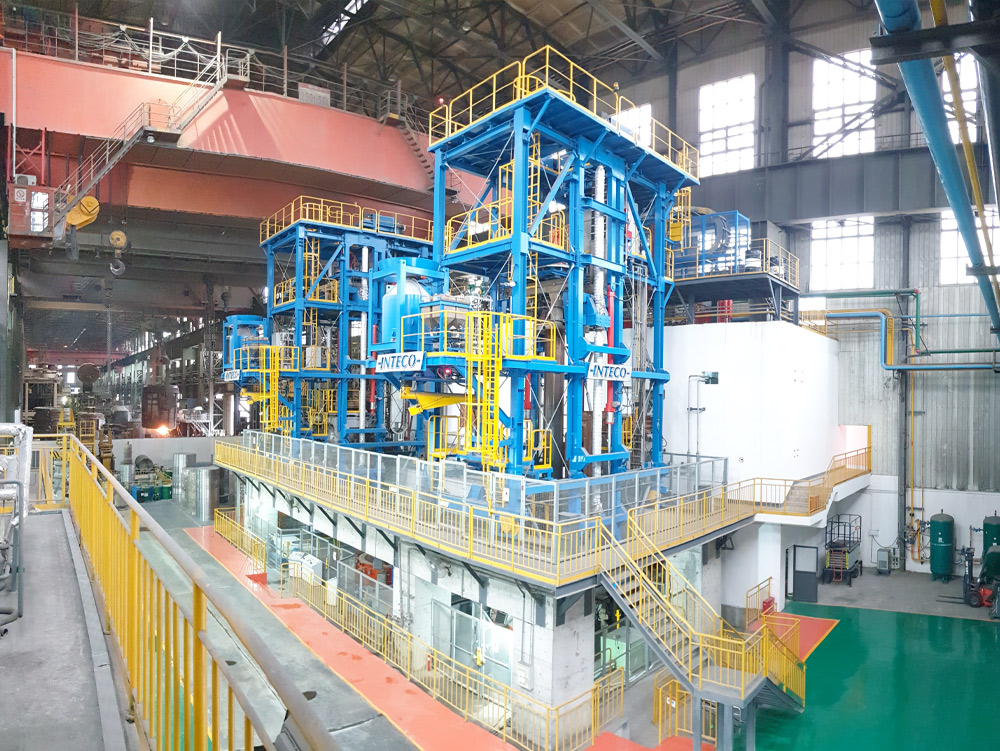
Erzhong
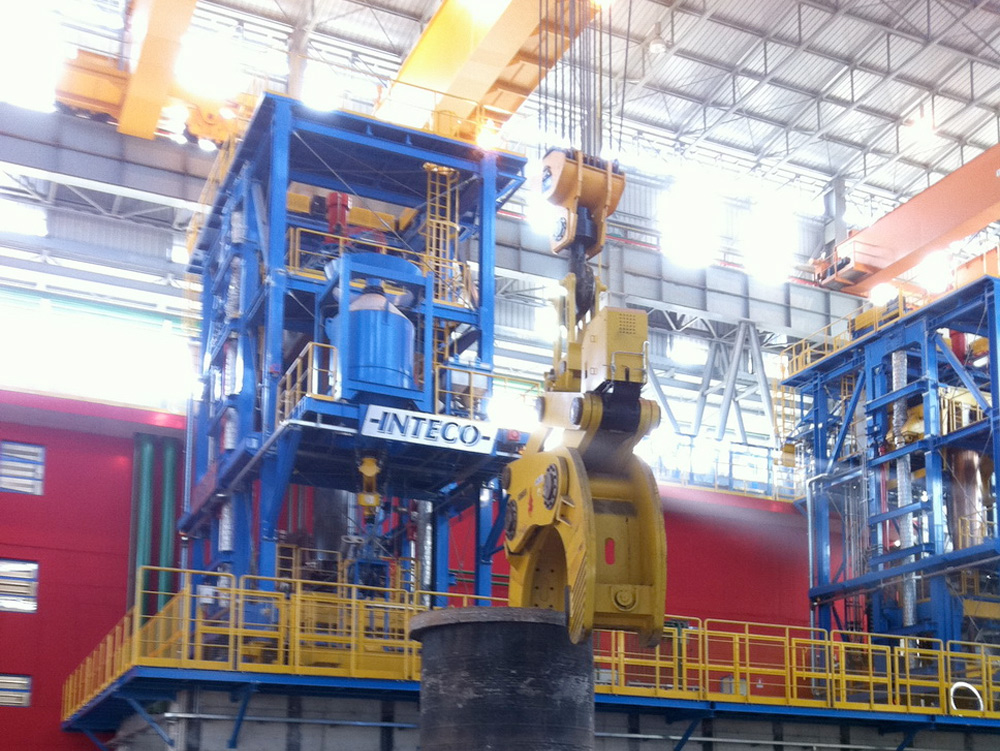