CONTINUOUS CASTING
- General information
- Variations
- Our technology – your advantage
- Digitalization
In recent decades, continuous casting has become the leading process for producing high-quality semi-finished steel products. The growing rise in products manufactured by continuous casting is attributable to the significant reduction in production costs and the simultaneous increase in the quality of the cast products. Considering the fact that approx. 95% of global crude steel is currently being produced using the continuous casting process, this process is very important for INTECO and its market positioning.
With the gradual integration of TBR, a company with over 30 years of experience in continuous casting, combined with the expertise of INTECO’s engineers, a competence center in the continuous casting sector was established nearly 15 years ago.
Today, this division represents an important part of the INTECO Group. INTECO is proud to be able to supply industrially established continuous casting technologies for casting blooms, billets, and beam blanks.
With continuous casting plants for special applications, such as horizontal or vertical continuous casting plants, INTECO offers solutions for all types of casting formats.
- Bow type or vertical bending/unbending machines
- Beam blank caster
- Horizontal casting machine
- Vertical casting machine / segment caster
- Tundish inertization
- Advanced and in-house developed solutions for mould level control (MLM—Mould Level Master)
- Hydraulic or servo-drive oscillator
- Dynamic secondary cooling control coupled with online solidification model
- Continuous bending/straightening
- Dynamic mechanical soft reduction (MSR) coupled with online solidification model
- Flexible electromagnetic stirring systems
- Rigid cooling bed for controlled cooling
- Level 2 / solidification and soft reduction control models
Digitalization and smart production are transforming the steel industry, driving development and change. At INTECO, we offer not only first-class engineering in plant construction, but also customized digital solutions tailored to our customers’ demands. Enhance your production with our digital solutions and utilize the collected data to make strategic adjustments and drive continuous progress.
The INTECO heating controller for EPH and ESH is a sophisticated solution for tundish heating. The basic design offers a cascaded control function for temperature control based on a fixed value or a temperature profile. It features automatic slag melting, immersion depth control and detection of stirring problems. Optionally, a temperature and prediction model can be applied using tundish condition and history as well as data of successful heat levels for predicting and controlling the temperature and making the system independent from a temperature signal.
The INTECO Oscillation Master uses a universal platform for all section sizes that can be used for hydraulic cylinders and servo drive oscillation systems. The servo drive oscillation’s eccentric drive is powered by a backlash free servo-drive, while the oscillating movement is achieved by alternating the servo-drive’s rotation direction. The frequency, stroke and shape of the oscillation movement can be adjusted online using the variable rotation angle. The actuator is exchangeable for flexibility and maintenance. With a servo-drive, high accelerations are feasible.
INTECO’s mould width adjustment system allows online adjustment of the mould width during casting and works with both INTECO mould designs as well as existing moulds with electromechanical or hydraulic cylinders. It features non-parallel adjustment to reduce stress on the strand shell and to minimize the transition length.
INTECO’s Break Out Prevention System (IBOPS) automatically detects and prevents liquid breakouts during the casting process which helps to reduce costly shutdowns. The system is based on classical algorithms and combines it with an AI-based system to improve the detection rate and to decrease false positives. Additionally, the AI-based system improves its effectiveness over time by utilizing historic trend data.
INTECO’s advanced online solidification model allows precise adjustment of the dynamic final stirrer’s position during the casting process and provides real-time data. It defines thermo-physical properties of steel according to the chemical composition and calculates temperature profiles along the entire solidifying strand. This allows to change input parameters such as casting speed, water flow, tundish heat, steel grade composition and many more. As a result, it ensures highest final product quality, guaranteeing high level of soundness, low segregation and defect-free center structure.
The Tundish Level Master is used for automatic level control of the filling level in the tundish at a defined set point by monitoring the tundish gross weight (through the related weighing system) and controlling the ladle slide gate.
A stable mould level is essential for casting high-quality steel grades. The INTECO Mould Level Master is an advanced control system which uses a patented detection system to ensure exact mould level control throughout the entire continuous casting process, regardless of the conditions, variations and disturbances. It reduces the risk of overflow, which results in better casting stability and a safe and reliable operation. The included flushing function removes clogging (alumina build-up). The system is sensor-independent and can be connected to various measuring systems such as radiometric, ultra-sonic, or eddy-current systems.
The soft reduction model can be easily linked to the solidification model to determine the optimal reduction amount depending on the solid fraction. Additionally, our secondary cooling optimization model uses the temperature data from the solidification model to control each cooling zone according to a defined temperature profile.
Our micro-segregation model defines thermo-physical properties of steel according to the chemical composition such as liquidus/solidus temperature, density and thermal conductivity. The solidification model calculates the temperature profiles along the entire solidifying strand, taking the thermal boundary conditions and relevant process variables like casting speed and water flow into consideration. The model provides real-time data on surface temperature, internal gradients and shell thickness as a function of solid fraction.
IMAS-PA-CC provides advanced top-down process guidance through dynamic or static treatment planning and integrated optimization tools. Process supervision is massively improved by the cockpit view and integrated real-time process models. IMAS provides instant real-time information and alerts, based on which the operators can control and steer the process just-in-time. The heat-based data recording stores sensor data, including complex information such as video streams, allowing observation of real-time data for quality assurance and process improvement.
PROJECTS
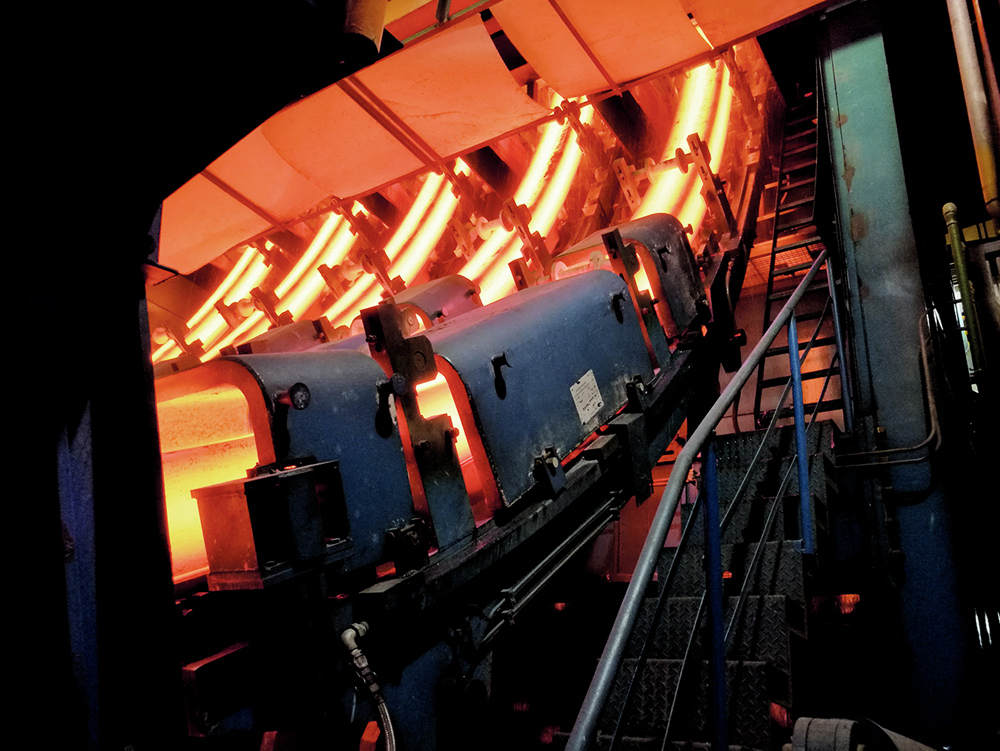
Shagang Group
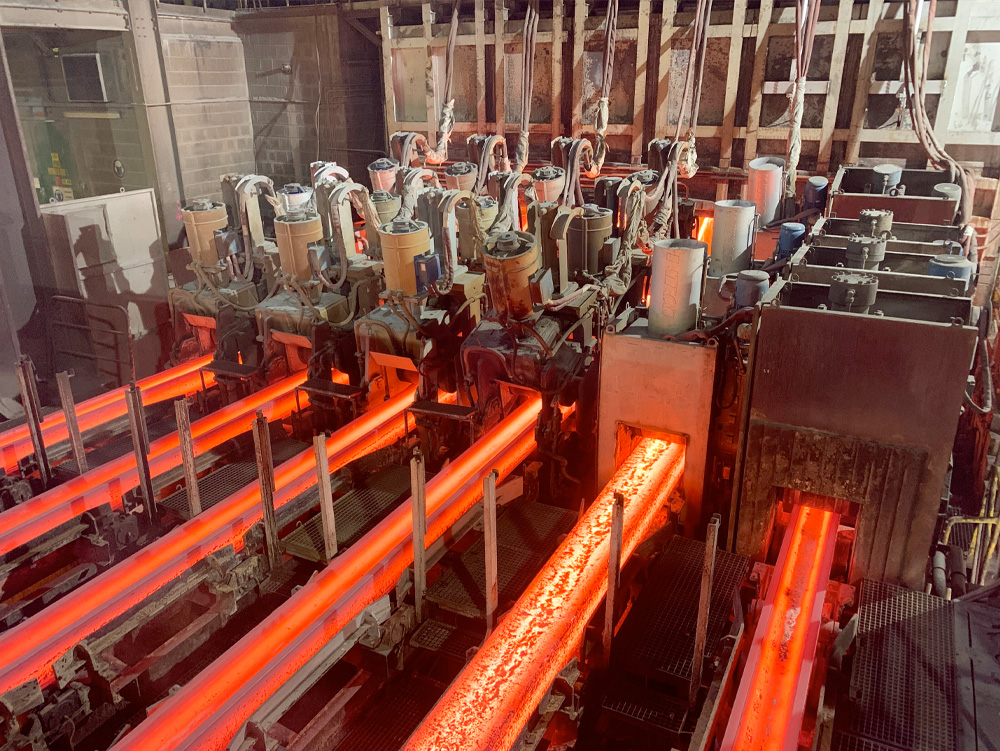
Arcelor Mittal Belval
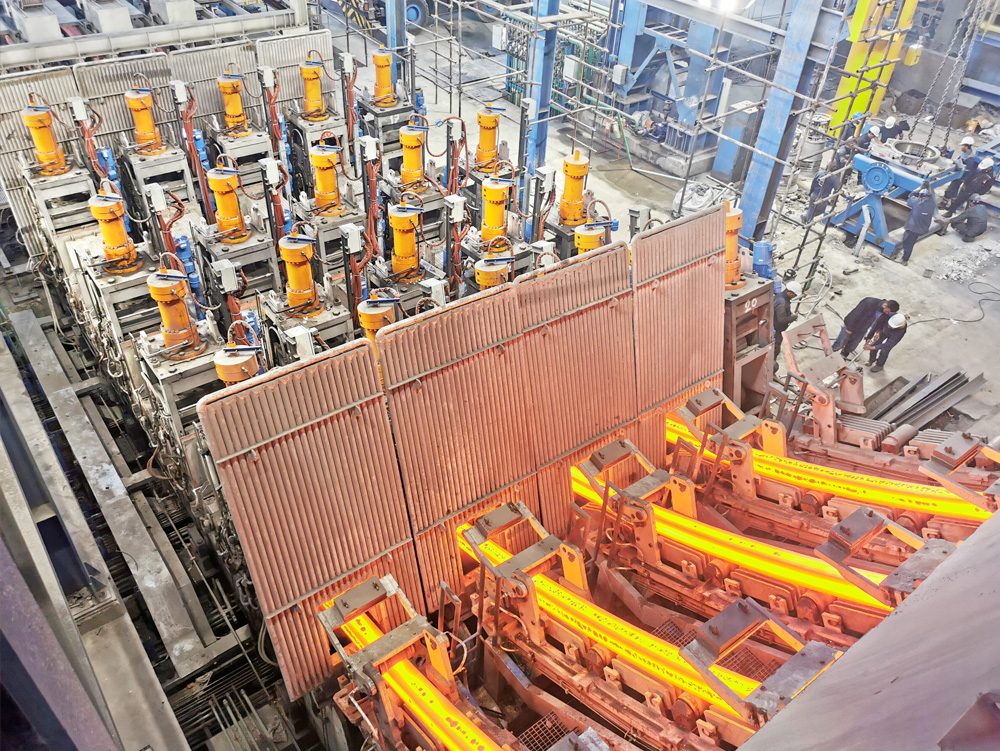
Confidential customer
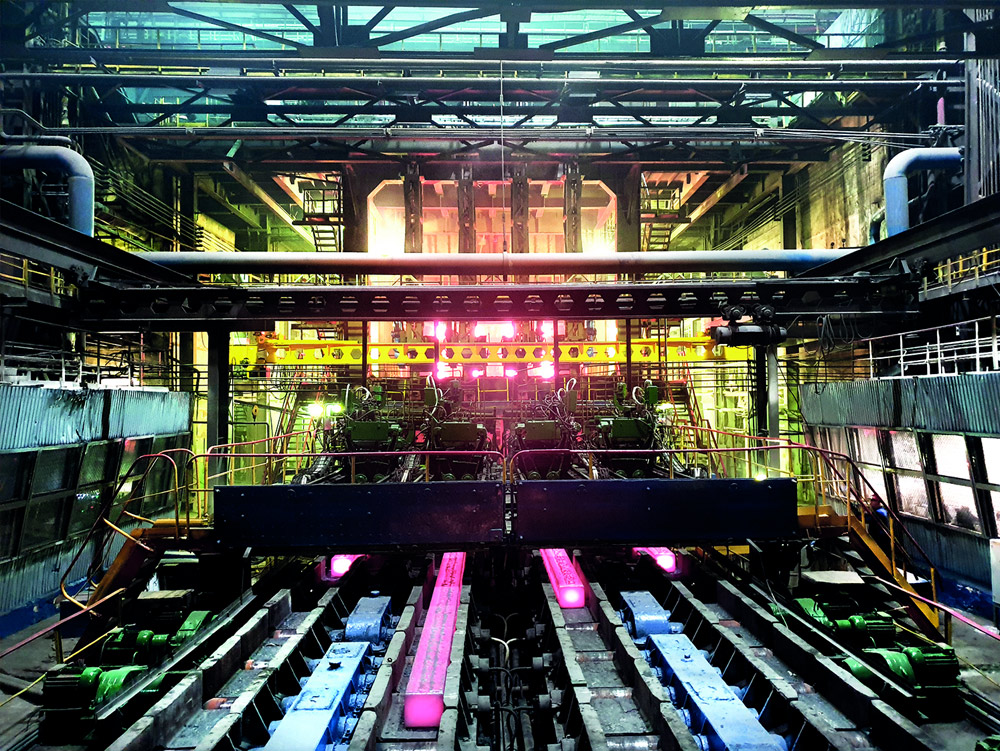